Analiza trwałości zmęczeniowej dla obudowy wentylatora chłodnicy w środowisku Simcenter 3D
Zmęczenie (materiału) jest to uszkodzenie spowodowane przez powtarzającą się zmianę naprężenia lub odkształcenia w materiale, w efekcie czego powstaje mikroskopijne pękniecie zwane punktem inicjacji, który powiększa się z każdym kolejnym cyklem. Prekursorem pierwszych badań zmęczeniowych był niemiecki inżynier kolejnictwa August Wöhler. Prowadził on badania cykliczne osi kolejowych w naturalnej skali, a także w małej skali próbek poddanych zginaniu, skręcaniu, ściskaniu i rozciąganiu dla kilku różnych materiałów. Wyciągnął bardzo ważne wnioski i wprowadził pojęcie granicy trwałości zmęczeniowej. Granica ta określa najwyższy poziom cyklicznego naprężenia, który nie powoduje zniszczenia próbek poddanych badaniu.
Wiele czynników wpływa na zmęczenie materiału, np. temperatura, środowisko pracy czy częstotliwość. Najczęściej w analizach opartych na metodzie elementów skończonych przeprowadza się obliczenia zmęczeniowe w celu oszacowania liczby cykli do zniszczenia, a co za tym idzie, uniknięcia efektu pojawienia się pęknięcia. Firma Siemens dostarcza dwa rozwiązania umożliwiające obliczenia trwałości zmęczeniowej. Pierwsze z nich, zaimplementowane w środowisku Simcenter 3D zapewnia możliwość obliczeń trwałości zmęczeniowej do pojawienia się propagacji pęknięcia; jest to najbardziej popularna metoda i najczęściej stosowana np. w lotnictwie czy przemyśle samochodowym. Druga metoda daje możliwość rzeczywistej analizy propagacji pęknięcia dzięki algorytmowi XFEM współpracującym z solwerem SAMCEF zaimplementowanym w środowisku LMS Virtual LAB.
Analiza trwałości zmęczeniowej w środowisku Simcenter 3D (NX CAE) zaprezentowano na przykładzie obudowy wentylatora chłodnicy silnika samochodowego (rys. 1). Istotne dane, potrzebne do oszacowania trwałości zmęczeniowej oraz główne etapy przedstawiono na rys. 2.

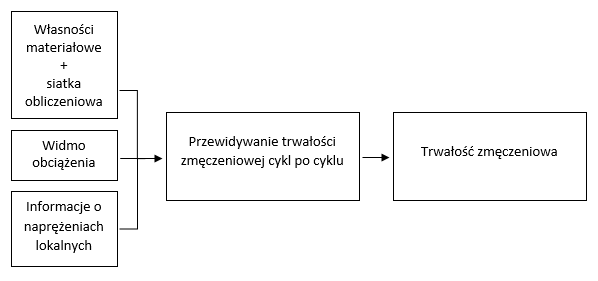
Własności materiałowe oraz siatka obliczeniowa
Przy realizacji procesu trwałości zmęczeniowej nie wystarcza scharakteryzowanie materiału za pomocą modułu Younga i współczynnika Poissona. Analiza trwałości zmęczeniowej modelowana jest zwykle przy zastosowaniu krzywych naprężenie-żywotność (S-N) lub odkształcenie–żywotność. W wielu przedsiębiorstwach najczęściej stosowana jest krzywa S-N. Takie podejście było stosowane w latach 70`- 80`. Zastosowanie w przemyśle nowej metody obliczeniowej skutkowało zgromadzeniem dużej ilości krzywych typu S-N, dlatego taką użyto w niniejszym artykule do przeprowadzenia analizy. Wykres zastosowanej krzywej S-N dla materiału polipropylen analizowanego wentylatora chłodnicy silnika samochodowego przedstawiono na rys. 3. Wykres zdefiniowano we własnościach materiału, w zakładce trwałość wprowadzając kolejno współrzędne punktów (rys. 4). Pozostałe własności materiałowe, użyte do analizy przedstawiono w tabeli 1.
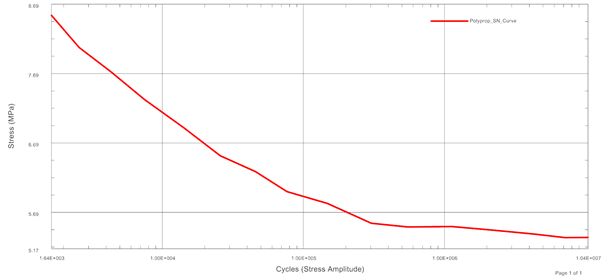
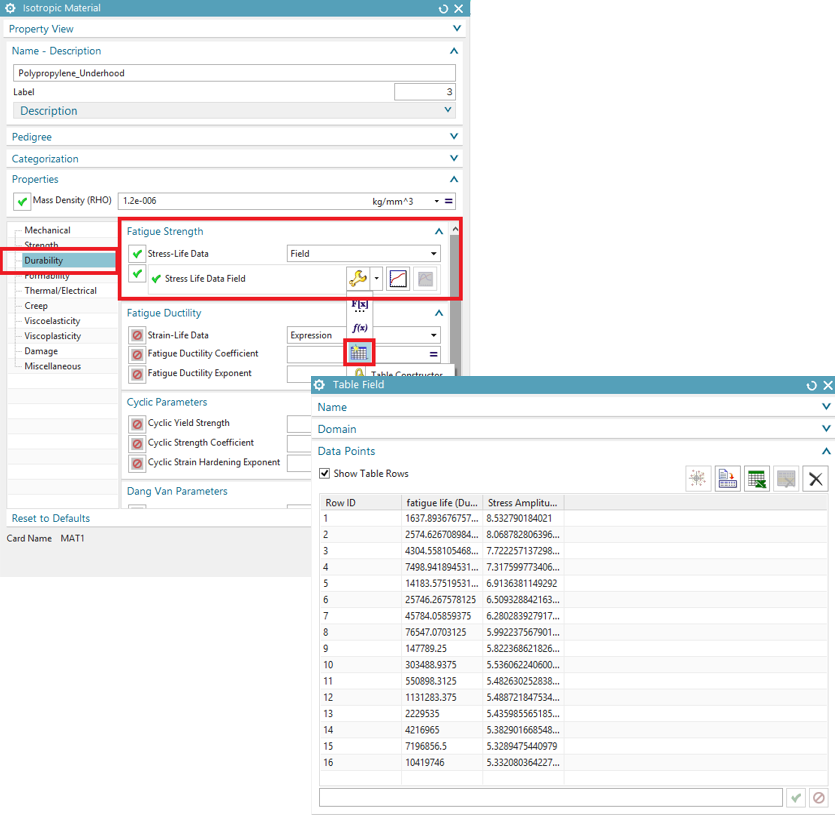
Tabela 1. Własności materiałowe
Gęstość właściwa ρ |
1.2e-006 |
kg/mm^3 |
Moduł Younga E |
200 |
MPa |
Współczynnik Poissona ν |
0.4 |
|
Granica plastyczności Re |
31 |
MPa |
Wytrzymałość na rozciąganie Rm |
75 |
MPa |
Na podstawie geometrii utworzono powierzchniową siatkę 2D wraz z elementami masowymi 0D o zadanej masie, imitującymi wiatraki oraz elementy łączące 1D (RBE2) co przedstawiono na rys. 5.

Warto również wspomnieć, że oprogramowanie Simcenter 3D posiada własną bibliotekę materiałów, w których zdefiniowano parametry potrzebne do analizy zmęczeniowej. Biblioteka ta posiada około 50 przykładowych materiałów i można ją znaleźć najczęściej w folderze instalacyjnym oprogramowania Siemens. W moim przypadku ścieżka ta wyglądała następująco:
C:Program FilesSiemensSimcenter 11.0NXCAE_EXTRASadvanceddurability
Przykład materiałów zaimportowanych z powyższej biblioteki widoczny w środowisku Simcenter 3D przedstawiono na rys. 6.

Naprężenia lokalne oraz widmo obciążenia
W celu uzyskania naprężeń lokalnych oraz rzeczywistego widma obciążenia, należy wykonać analizy MES w taki sposób, aby odzwierciedlić rzeczywistą pracę konstrukcji z uwzględnieniem wszystkich sił np. z uwzględnieniem obciążenia gnącego oraz skręcającego z uwzględnieniem analizy w czasie (transient). Proces ten jest często długotrwały, dlatego mamy możliwość przeprowadzenia obliczeń w stanie ustalonym oraz przeskalowania naszego obciążenia zgodnie z odpowiednim cyklem pracy. Do cykli obciążenia można zaliczyć cykle ustalone (cykliczne) i nieustalone. W przypadku cykli symetrycznych mamy do czynienia z wykresami Wöhlera, natomiast dla cykli niesymetrycznych najczęściej posługujemy się krzywą Haigha Goodmana.
W przypadku konstrukcji obudowy wentylatora, naprężenia lokalne, które powstały podczas pracy konstrukcji zostały uwzględnione z analizy drgań własnych. W tym celu utworzono rozwiązanie SOL 103 Dynamika Reakcji (rys. 7). Zastosowano następujące warunki brzegowe – więzy użytkownika odbierając pojedynczemu węzłowo wszystkie obrotowe stopnie swobody (Rx, Ry, Rz) – rys. 8.
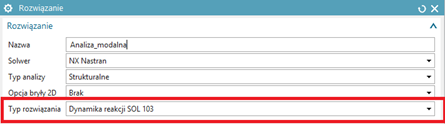
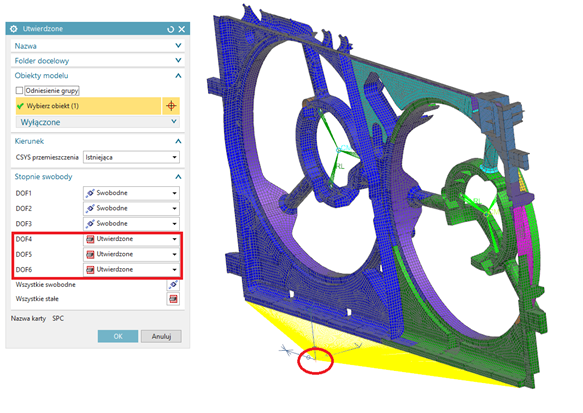
Pojawia się kluczowe pytanie, dlaczego nie wybrano rozwiązanie przeznaczonego do drgań własnych SOL 103 – rzeczywiste wartości własne. Odpowiedź ta jest bardzo istotna, po wykonaniu drgań własnych przeprowadzono analizę drgań wymuszonych z rzeczywistym widmem obciążenia, które następnie użyto do analizy zmęczeniowej. Podmoduł przeznaczony do analiz drgań wymuszonych współpracuje z rozwiązaniem SOL 103 Dynamika reakcji. Dodatkowo, aby móc zainicjować w późniejszym etapie efekt drgań wymuszonych, przypisano do tego samego węzła warunek brzegowy – Wymuszone położenie ruchu (Wzbudzenie), rys. 9.
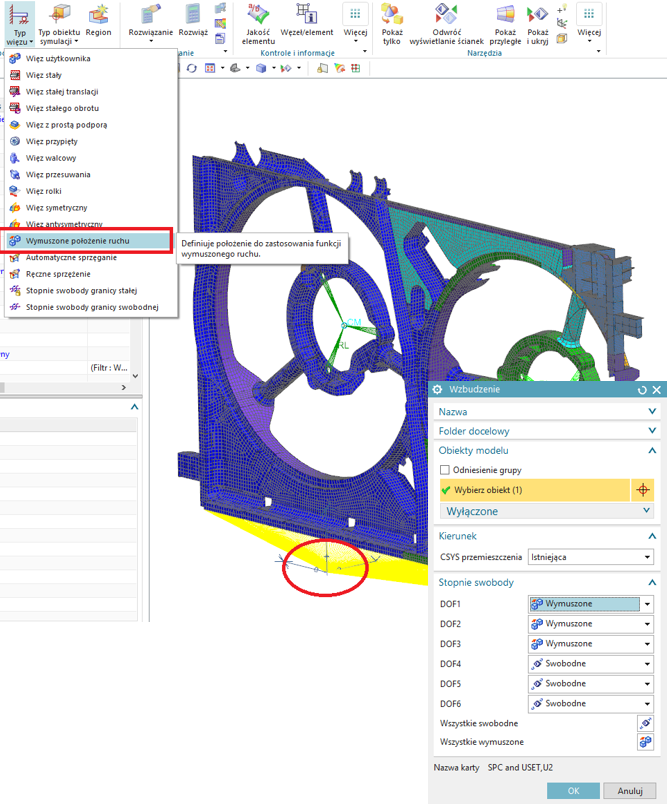
Dla tak przypisanych warunków brzegowych, przeprowadzono symulację otrzymując pierwszych dwadzieścia częstotliwości drgań własnych. Przykładowe wartości przemieszczeń dla częstotliwości 1 przedstawiono na rys. 10.

Jedną z najmocniejszych stron środowiska Simcenter 3D są analizy statyczno – dynamiczne, w których skład wchodzą:
- Wymuszenie częstotliwościowe (harmoniczne)
- Wymuszenie spowodowane uderzeniem
- Losowe (PSD – widmowa, gęstość mocy)
- Rotor – dynamic
- Analiza akustyczna – wibroakustyczna
W oparciu o drgania własne przeprowadzono analizę statyczno – dynamiczną w formie drgań wymuszonych. Wykorzystano do tego celu zakładkę Dynamika reakcji z poziomu pliku symulacyjnego (rys. 11).

Zdefiniowano nowa analizę dynamiczną klikając nową dynamikę reakcji (rys. 12). W nowo otwartym oknie dialogowym dynamiki reakcji można zauważyć, że program pobiera dane rozwiązania, które już zostało przeprowadzone poprzednio (drgania własne) do dalszej analizy drgań wymuszonych. Wprowadzono tolerancję obiektu sztywnego wynoszącą 0,001 Hz (rys. 13).


Z poziomu nawigatora symulacji rozwinięto zakładkę Widok szczegółów dynamiki reakcji, zmieniając procentową wartość tłumienia wiskotycznego z 0 na 2 % dla wszystkich częstotliwości drgań własnych (rys. 14).
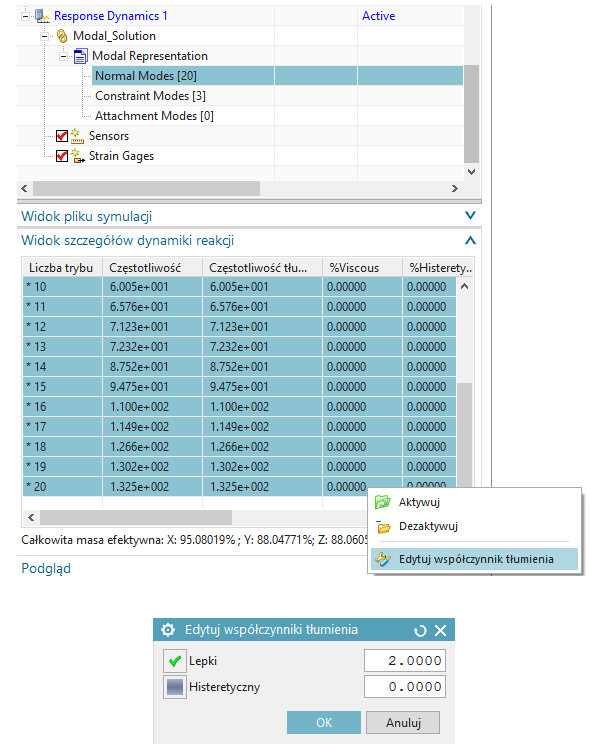
Zdefiniowano nowe wymuszenie klikając nowe krótkotrwałe zdarzenie w nawigatorze symulacji na Resposonse Dynamics 1 (rys. 15).
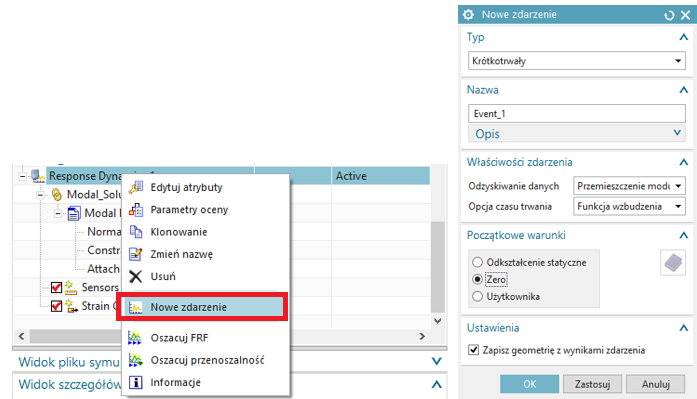
Poniżej ukazano widmo obciążenia zmierzone na rzeczywistym modelu i zaimplementowane do środowiska Simcenter 3D. W skład rzeczywistego widma wchodzą wykresy przemieszenie w funkcji częstotliwości oraz przemieszczenie w funkcji czasu (rys. 16).

Dla utworzonego zdarzenia zdefiniowano nowe wzbudzenie węzła klikając na Event_1, nowe wzbudzenie, następnie wybierzmy polecenie – postępowe węzłowe (rys. 17).
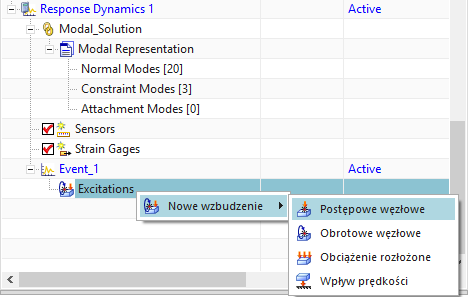
W nowo otwartym oknie dialogowym należy zdefiniować wzbudzenie naszego węzła. Z listy wybieramy węzeł, dla którego wcześniej użyliśmy warunek wzbudzenia oraz należy zdefiniować wymuszenie węzła w wybranych kierunkach (rys. 18 – 19). Wykorzystano rzeczywiste przebiegi, które wcześniej przedstawiono i zaimplementowano do środowiska Simcenter 3D.
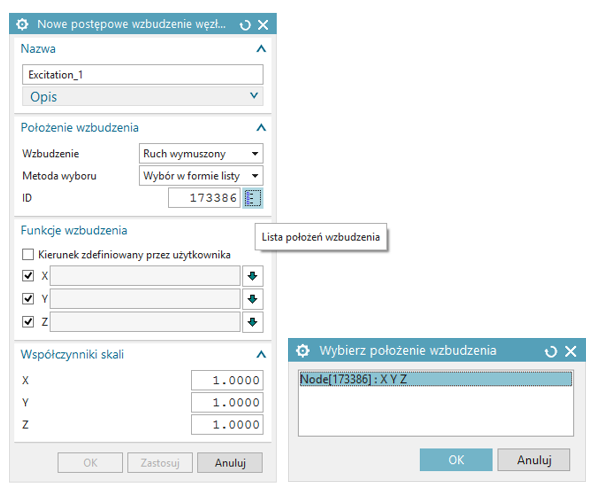
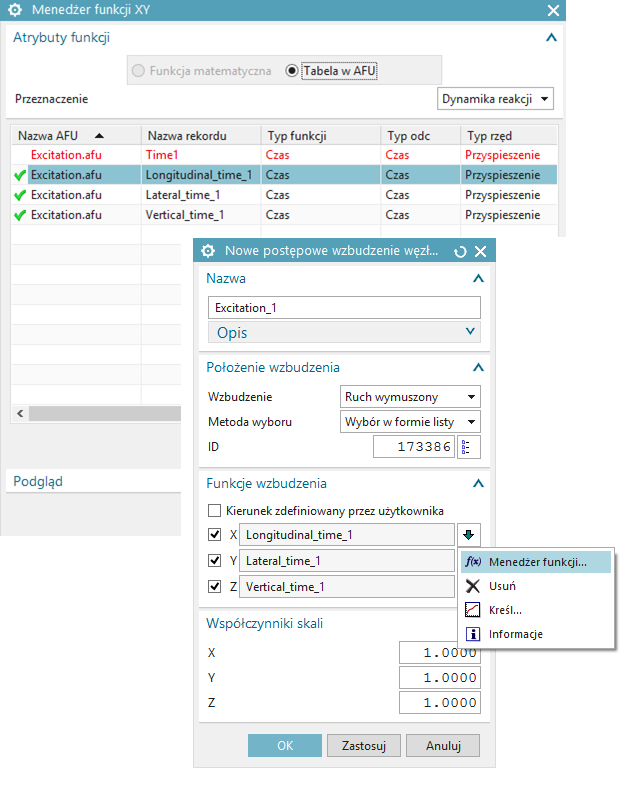
Przeprowadzono obliczenia dla drgań wymuszonych klikając w Event_1, rozwiąż dla reakcji modalnej (rys. 20).
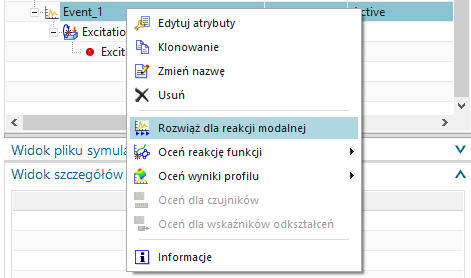
W kolejnym etapie utworzono nową analizę trwałości zmęczeniowej. W tym celu w głównym pasku wstęgowym wybrano zakładkę Trwałość (rys. 21).

Utworzono nową analizę zmęczeniową wybierając w zakładce Trwałość polecenie Nowa symulacja zmęczeniowa (rys. 22). W nowo otwartym oknie dialogowym należy zdefiniować nazwę analizy. Po utworzeniu nowej nazwy analizy zmęczeniowej w oknie nawigatora symulacji pojawi się aktywna utworzona analiza zmęczeniowa (rys. 22).
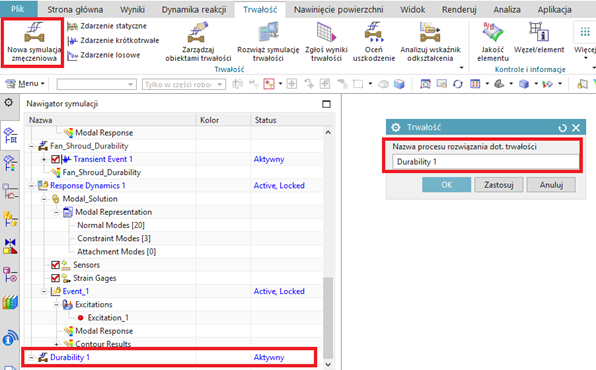
Dla utworzonej analizy zmęczeniowej Durablity 1 utworzono nowe zdarzenie krótkotrwałe, które pochodzi z rzeczywistego widma obciążenia, uzyskanego wcześniej z analizy drgań wymuszonych (rys. 23).
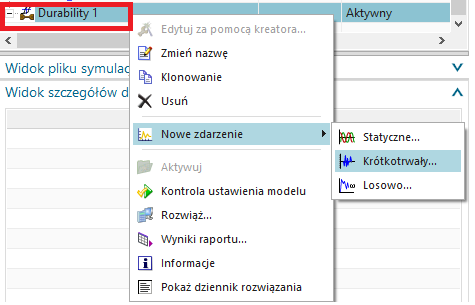
W czasie tworzenia nowego zdarzenia krótkotrwałego należało zdefiniować odpowiednie parametry dla analizy zmęczeniowej. Do parametrów tych należało:
Kryterium trwałości zmęczeniowej: Stress_Life
Model cyklicznych naprężeń odkształceniowych: Ramberg-Osgood
Liczba elementów w pętli histerezy: 100
Cykli do uszkodzenia: 1e+006
Wyjście współczynnika wytrzymałości zmęczeniowej: Goodman
Kryterium naprężenia: Ultimate
Typ naprężenia: Von_Mises
Dla tak zdefiniowanych parametrów przeprowadzono obliczenia zmęczeniowe. Wyniki konturów liczby cykli do zniszczenia przedstawiono na rys. 24. Z wyników obliczeń można jasno określić punkt, w którym nastąpi możliwość propagacji pęknięcia oraz oszacować liczbę cykli, przy których to pękniecie się pojawi. W naszym przypadku jest to ważne ponieważ w wielu gałęziach przemysłu np. w lotnictwie nie chcemy doprowadzić do momentu wystąpienia pęknięcia, ale już wcześniej zareagować i oszacować wytrzymałość zmęczeniową naszej konstrukcji.
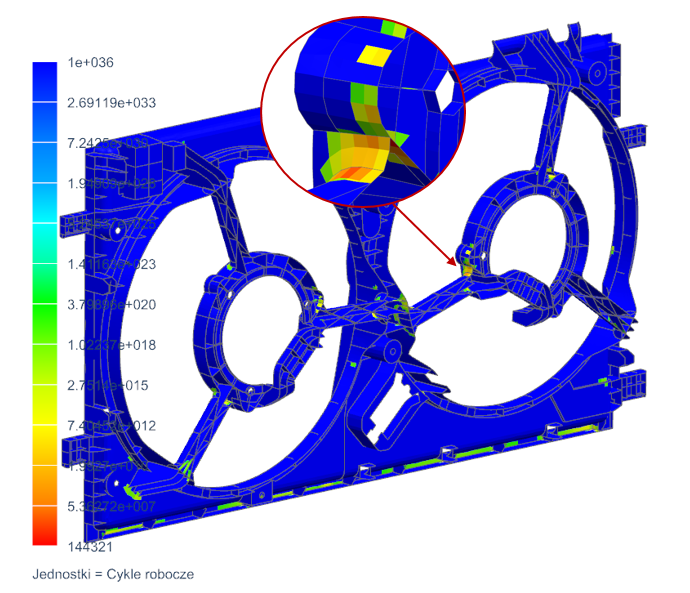
Analiza trwałości zmęczeniowej w Simcenter 3D na filmie
W celu lepszego zobrazowania procesu wykonywania analizy trwałości zmęczeniowej obudowy wentylatora chłodnicy, przygotowaliśmy specjalny film:
Artykuł ten jest kolejną częścią naszego cyklu edukacyjnego MES. Szereg wcześniejszych tekstów oraz materiałów wideo znajduje się na naszym blogu i kanale YouTube. Jeśli jesteście zainteresowani poszerzeniem wiedzy z zakresu analiz w Simcenter 3D (NX CAE), zachęcam do kontaktu mailowego.
opracował
Marek Rudy
marek.rudy@gmsystem.pl