Ulepszone możliwości symulacyjne Moldex3D do precyzyjnego przewidywania zatonięć w wypraskach o skomplikowanej geometrii
We współczesnym przemyśle istnieje tendencja, aby produkty polimerowe miały coraz bardziej skomplikowany kształt, przy zachowaniu cienkich ścianek. Z tego względu niezwykle trudną kwestią jest zachowanie równowagi pomiędzy aspektami estetycznymi a integralnością strukturalną wyrobów. Dla zwiększenia wytrzymałości mechanicznej wyprasek często stosuje się liczne użebrowania, które mogą jednak przyczyniać się do powstawania defektów powierzchniowych w postaci zatonięć, wywołanych zwiększoną grubością tworzywa na połączeniu żeber ze ściankami. Poza kształtem geometrii, występowanie zatonięć jest ściśle związane z warunkami występującymi w procesie wytwórczym podczas fazy docisku.
Przed upowszechnieniem się wykorzystywania symulacji komputerowych do optymalizacji parametrów procesu wtrysku, dobór warunków zapewniających właściwą redukcję zatonięć na wyrobie wymagał znacznego doświadczenia oraz wykonania licznych testów metodą „prób i błędów”. Ze względu na wspomniany wcześniej, wysoki stopień skomplikowania geometrii oraz konieczność szybkiego dostarczania nowych produktów na rynek, te tradycyjne metody stały się niewystarczające. Z tego względu Moldex3D, wiodący na rynku system do symulacji procesu wtrysku polimerów, dostarcza swoim użytkownikom bardzo użyteczną funkcjonalność – Sink Mark Displacement Analysis. Narzędzie to wykonuje w fazie docisku analizę procesu tworzenia zatonięć, bazując na podstawie geometrii detalu i rodzaju tworzywa, w efekcie precyzyjnie obliczając wartości przemieszczeń zapadających się powierzchni ścianek. Wyniki te stanowią wartościowe informacje, przydatne do optymalizacji kształtu produktu oraz parametrów procesu, na długo przed rozpoczęciem prób fizycznych.
Poniżej zaprezentowane zostaną przykłady analizy zatonięć wykonanych w programie Moldex3D. W celu zbadania skuteczności wykrywania tego typu wad, przygotowano model geometryczny zawierający płaską powierzchnię z czterema żebrami o różnej grubości: 1.8 mm, 1.5 mm, 1.2 mm i 0.9 mm (rys. 1).

Wyniki analizy rozkładu skurczu objętościowego w fazie docisku (rys. 2) przedstawiają równomierną wartość skurczu w płaskiej ściance detalu. Jednak w obszarach, w których żebra łączą się ze ścianką, można zauważyć nierównomierność skurczu. Im większa grubość żebra, tym większe wartości skurczu można zaobserwować, co daje większą szansę na wystąpienie zatonięcia w tych miejscach.

Na rys. 3 przedstawiono wyniki analizy Sink Mark Displacement z wyraźnie zauważalnymi obszarami zatonięć oraz widok rzeczywistego detalu, który potwierdza prawidłowość przeprowadzonej symulacji.
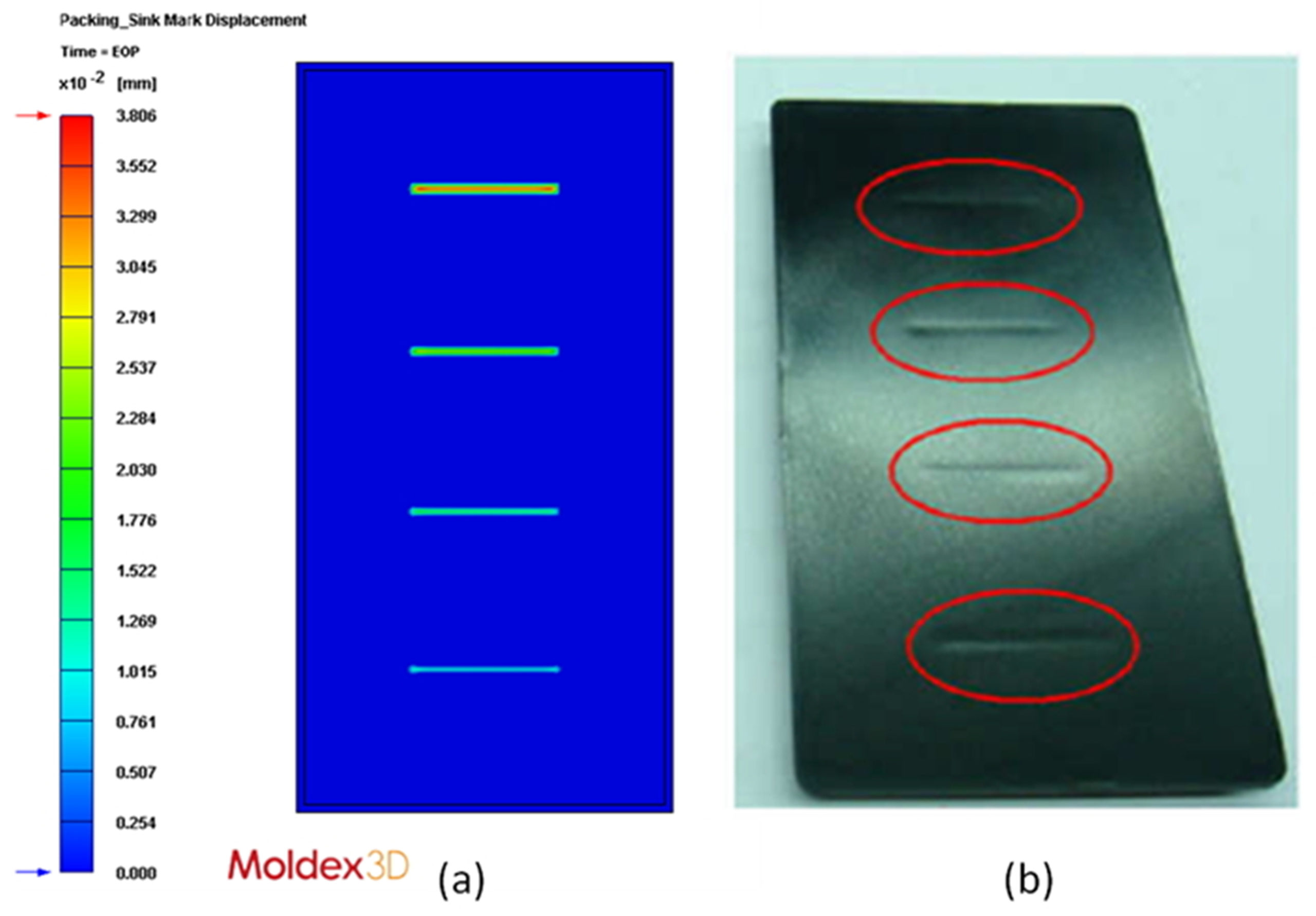
Funkcjonalność analizy zatonięć jest w Moldex3D nieustannie doskonalona dla lepszego przewidywania tego typu wad w detalach o skomplikowanej geometrii. Na rys. 4 przedstawiono model zawierający żebra umieszczone pod różnym kątem. Wyniki analizy skurczu objętościowego pokazują jego nierównomierny rozkład, co może sugerować możliwość wystąpienia zatonięć na powierzchni wyrobu.

Wcześniejsze wersje Moldex3D nie zawsze prawidłowo interpretowały tego typu geometrię podczas analizy zatonięć. Na rys. 5 przedstawiono porównanie wyników pomiędzy najnowszą i poprzednią wersją programu. Można zauważyć, że możliwości wykrywania zatonięć zostały znacząco ulepszone. Ilustracja 5b potwierdza, że Moldex3D jest w stanie prawidłowo przewidywać zatonięcia, nawet w miejscach, w których zastosowano pochylone żebra.
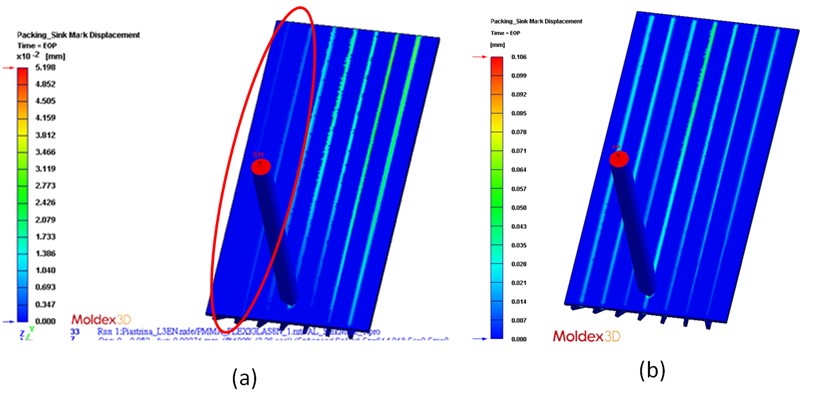
Ulepszenia dokonane w zakresie analizy zatonięć stanowią niezbity dowód, że Moldex3D jest nieustannie rozwijany w celu zwiększania możliwości i dokładności przeprowadzanych symulacji. Zapewnia to znaczące korzyści dla jego użytkowników podczas projektowania detali polimerowych, zwłaszcza tych o skomplikowanej geometrii. Moldex3D pozwala wykrywać potencjalnie problematyczne obszary wyprasek i sprawdzać skuteczność zastosowanych zabiegów naprawczych, przyczyniając się tym samym do redukcji liczby kosztownych prób fizycznych oraz skracając czas wprowadzania nowych produktów na rynek.
opracował
Piotr Menchen
piotr.menchen@gmsystem.pl