Wykorzystanie Moldex3D do optymalizacji wytwarzania polimerowych części motoryzacyjnych
W branży motoryzacyjnej wykorzystywanych jest wiele elementów z tworzyw polimerowych. Stawiane są im wysokie wymagania jakościowe, zarówno pod względem wymiarowym, jak i wizualnym. Dla spełnienia tych wymagań niezwykle przydatne jest zastosowanie symulacji procesu wtrysku w systemie Moldex3D, pozwalające na wykrywanie i eliminowanie potencjalnych problemów przetwórczych już na wczesnych etapach projektowych.
W niniejszym artykule zaprezentowany zostanie przykład wykorzystania Moldex3D przez firmę Faurecia, światowego producenta części i systemów wyposażenia wnętrz samochodowych.
Jednym z projektów realizowanych przez firmę Faurecia była osłona konsoli centralnej (rys. 1). Ponieważ jest to element widoczny dla użytkownika pojazdu, stawiane mu były wysokie wymagania estetyczne. Defekty wizualne powierzchni, takie jak zatonięcia, linie łączenia czy ślady płynięcia, miały być ograniczone do minimum i występować tylko w mniej widocznych obszarach części. Należało również zminimalizować deformacje kształtu wypraski dla zapewnienia wysokiej precyzji wymiarowej, niezbędnej dla prawidłowego montażu tego elementu.
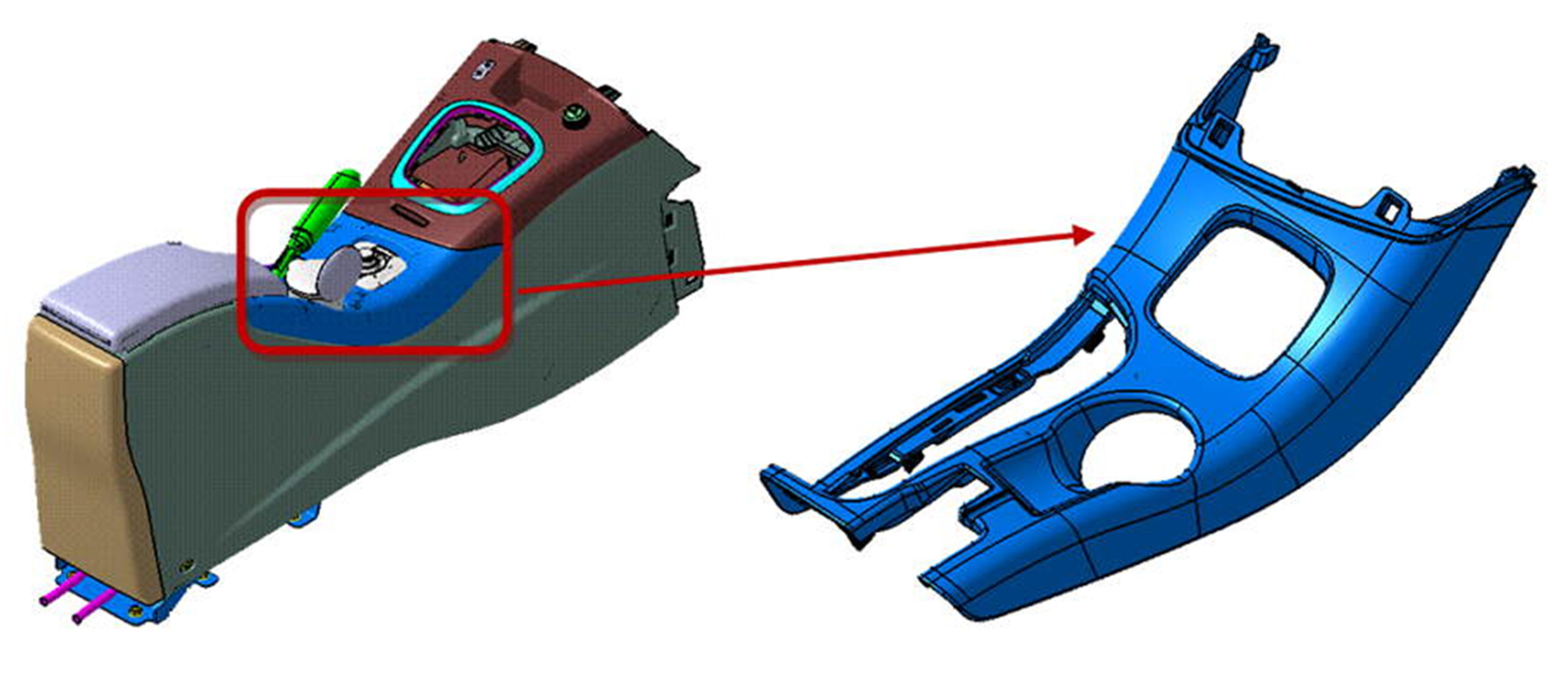
Postawione cele miały zostać osiągnięte poprzez działania zapobiegawcze podjęte na etapie projektowania i rozwoju produktu, zamiast wprowadzania kosztownych i czasochłonnych poprawek na etapie prób fizycznych formy. Było to możliwe dzięki zastosowaniu symulacji procesu wypełniania, docisku, chłodzenia i deformacji w oprogramowaniu Moldex3D w wersji eDesign.
Wyniki symulacji przeprowadzonej dla oryginalnego projektu osłony (rys. 2) pokazały, że na widocznej powierzchni detalu wystąpią linie łączenia (rys. 3), a wielkość deformacji może powodować nieprawidłowości podczas jego montażu. Ponadto zaobserwowano efekt przepakowania w rejonie przewężki, spowodowany wysokim zróżnicowaniem ciśnienia i temperatury, a także niedolew w jednym z cienkich żeber.
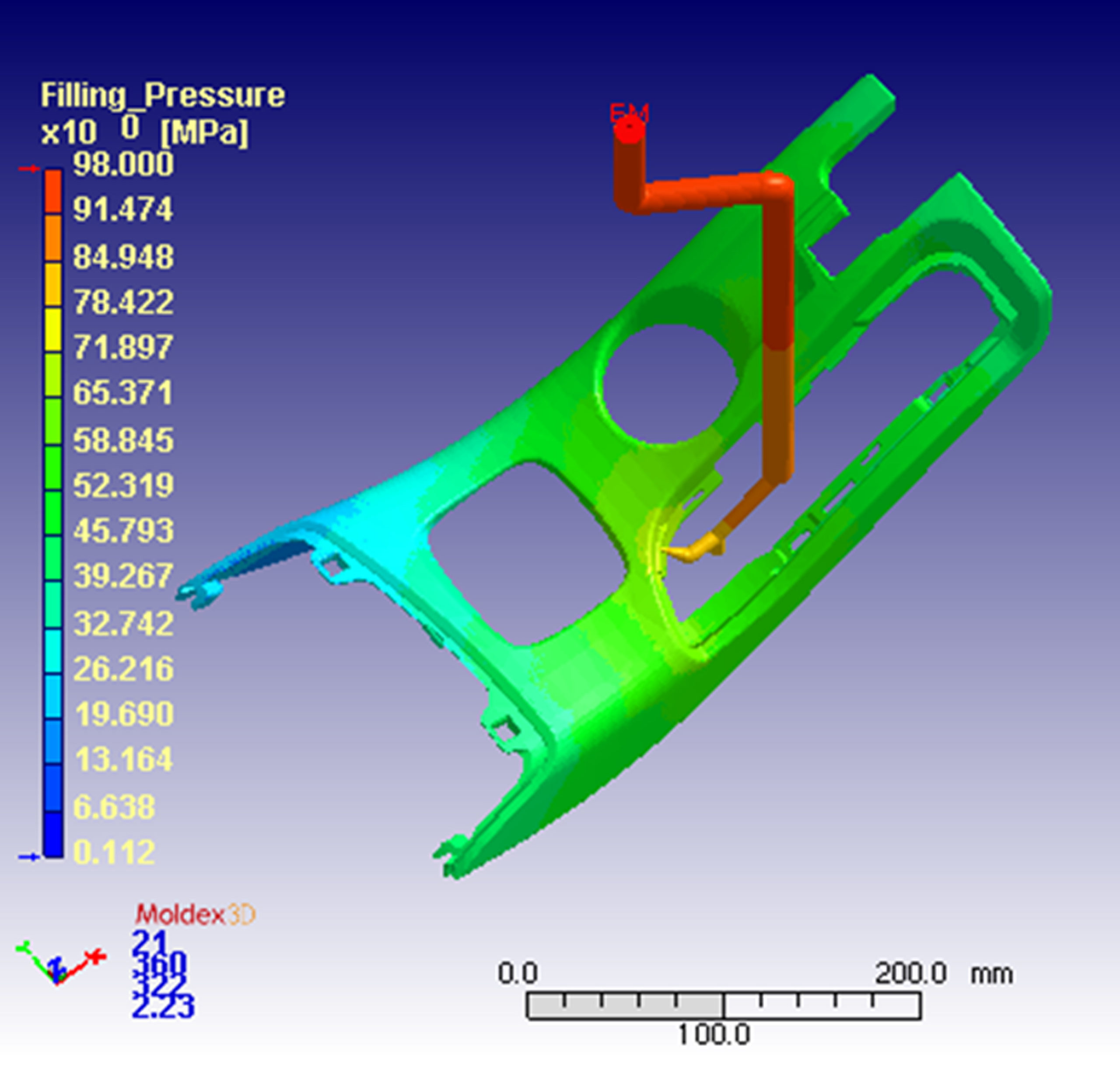

W celu rozwiązania wykrytych problemów postanowiono zastosować odmienny projekt układu wlewowego z jednoczesnym wprowadzeniem zmian w grubości ścian detalu. Zaproponowano zmniejszenie grubości ścian w obszarze wokół otworu (rys. 4), aby zmniejszyć odkształcenia w kierunku osi Y i Z. W układzie wlewowym dodano dodatkową dyszę gorącokanałową i zastosowano sekwencyjne sterowanie otwieraniem dysz. Zwiększono również liczbę punktów wtrysku poprzez przeprojektowanie zimnego wlewka (rys. 5).

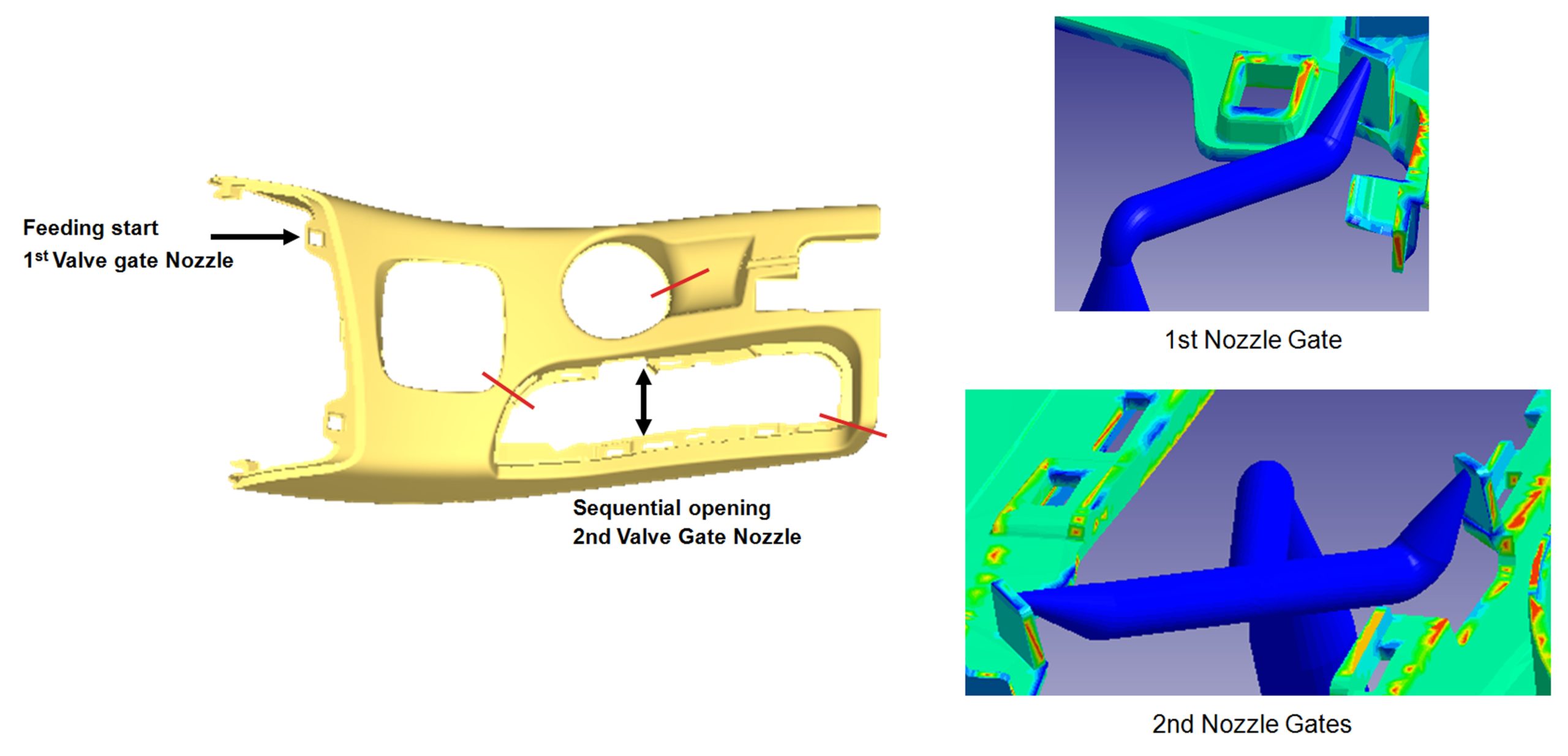
Po wprowadzeniu zmian dokonano kolejnej symulacji w celu weryfikacji ich efektów. Zaobserwowano znaczącą poprawę w kwestii położenia linii łączenia. Linie te znalazły się teraz w narożach detalu, które są mniej widoczne dla użytkownika (rys. 6).

Dla omawianego detalu przeprowadzono również badania mające na celu porównanie otrzymanych wyników symulacji z efektami rzeczywistych prób formy. Wyniki dotyczące rozpływu tworzywa i związanych z tym defektów powierzchni idealnie odpowiadały rzeczywistości (rys. 7 I 8).
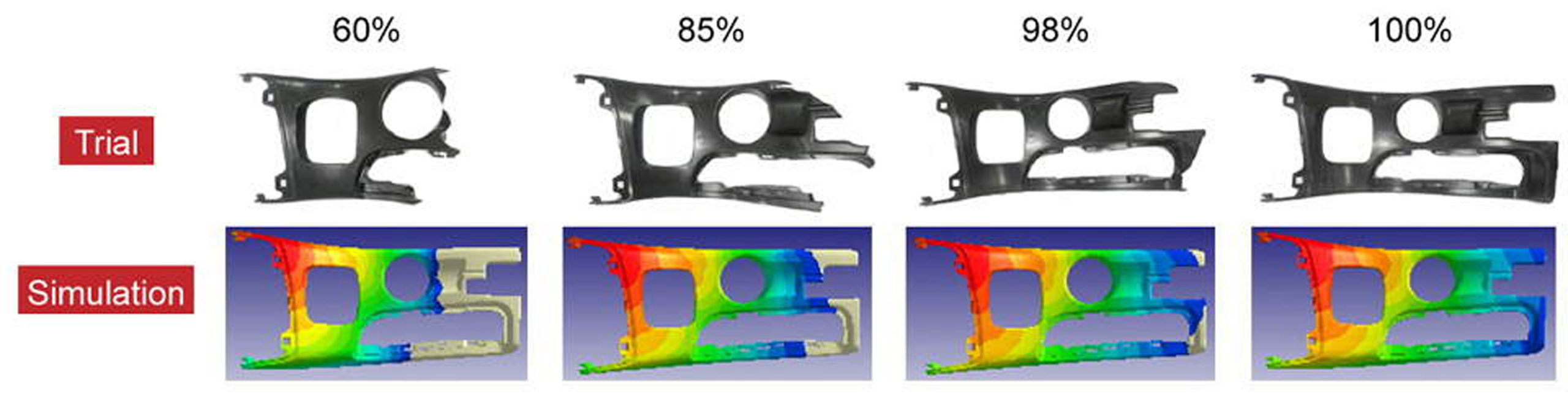
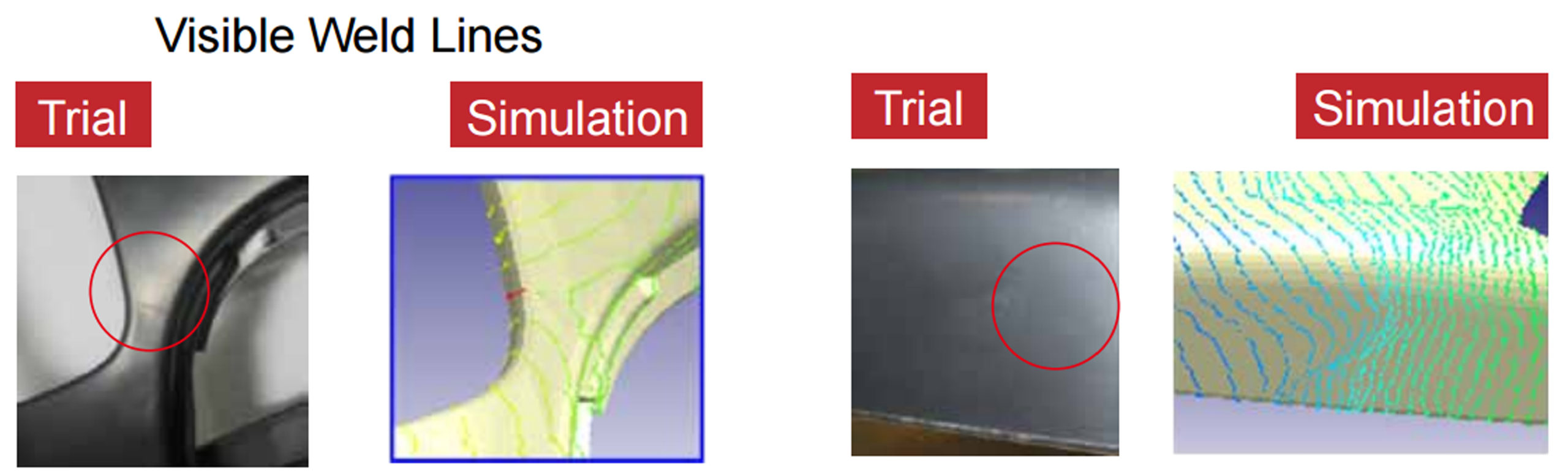
Wyniki deformacji otrzymane w symulacji również bardzo dobrze odpowiadały rzeczywistym efektom procesu wtrysku (rys. 9 i 10). W poprawionym projekcie można było zaobserwować znaczące zmniejszenie niekorzystnych odkształceń wypraski, co zapewniło możliwość spełnienia założonych wymagań wymiarowych.

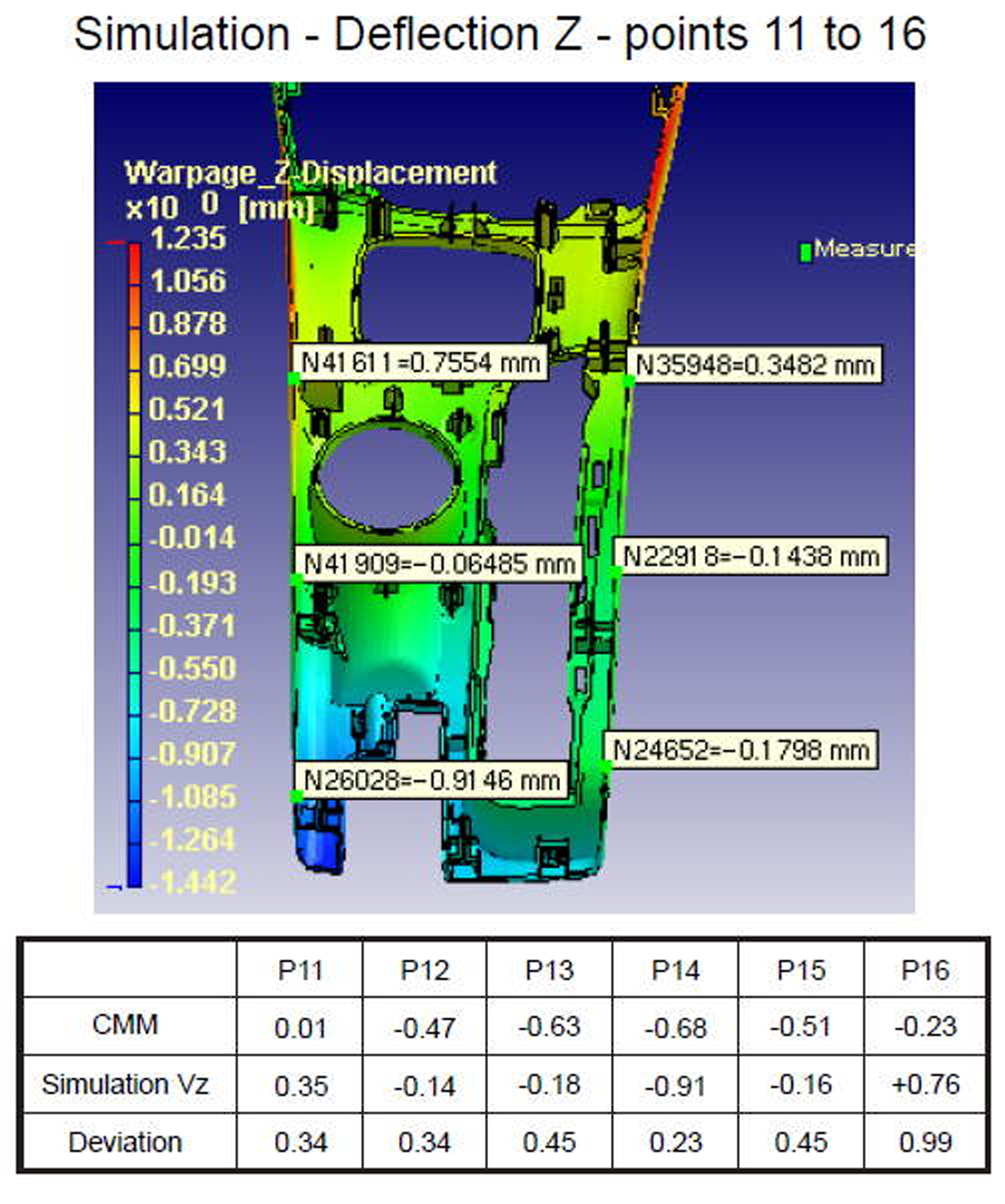
Precyzyjne wyniki symulacji wtrysku, wykonanej w Moldex3D, umożliwiły firmie Faurecia wykrycie potencjalnych problemów ze spełnieniem postawionych wymagań i wyeliminowanie ich już na wczesnym etapie projektu, bez potrzeby przeprowadzania wielu kosztownych prób fizycznych i poprawek. Skutkowało to redukcją kosztów optymalizacji formy aż o 68% w porównaniu z tradycyjnym podejściem opartym tylko na doświadczeniu i próbach fizycznych. Jak widać na opisywanym przykładzie, wykorzystanie symulacji wtrysku w systemie Moldex3D na wszystkich etapach procesu rozwoju produktu zapewnia skuteczną realizację nawet najbardziej wymagających projektów, przy znaczących oszczędnościach czasu i pieniędzy.
opracował
Piotr Menchen
piotr.menchen@gmsystem.pl