Poprawa wydajności obróbek za pomocą NX CAM – cz. 1
Część 1 – opcje HSM.
Technologia frezowania z dużymi szybkościami (ang. HSM – High Speed Machining, HSC – High Speed Cutting) zaimplementowana została w NX CAM głównie z przeznaczeniem prowadzenia obróbek wykańczających. Technologia ta stosowana jest przede wszystkim w obróbkach materiałów trudno skrawalnych, jak np. aluminium, czy w obróbkach materiałów twardych np. uzyskiwanych po obróbce cieplnej. Jej celem jest uzyskanie odpowiedniej jakości powierzchni obrabianej, co z kolei przekłada się na zwiększoną twardości warstwy wierzchniej (eliminując obróbkę cieplną) oraz na lepszą jej jakość (pamiętajmy, że uzyskanie odpowiedniej klasy dokładności obróbki, nawet w przypadku obróbki szybkościowej, to konieczność zgrania kilku czynników, co nie zawsze jest łatwe i proste do przewidzenia). To nie koniec zalet stosowania tej technologii, ponieważ wraz z podwyższeniem parametrów skrawania jesteśmy w stanie zredukować czas obróbek maszynowych, co ma bezpośredni wpływ na koszty produkcji, które jak wiemy, są istotnym elementem kształtującym cenę produktu.
Projektując obróbki frezowania z dużymi szybkościami należy pamiętać o kilku zasadach, których pominięcie może mieć negatywne skutki dla przebiegu całego procesu. Dlatego, projektując tego typu obróbki, powinniśmy zwracać szczególną uwagę na pewne aspekty, które w NX CAM znaleźć można pod pojęciami:
1. Wygładzanie
Opcję można znaleźć niemal w każdej operacji, niezależnie od modułu frezarskiego. Charakteryzuje się ona tym, że zamienia szybkie ruchy przejazdowe – generowane w domyślnych ustawieniach ostrym narożnikiem (rys. 1) – na płynne i smukłe ścieżki (rys. 2). Takie podejście pozwala ustabilizować pracę maszyny w aspekcie szybkich ruchów przejazdowych generowanych domyślnie z nastawami dającymi gwałtowne zmiany kierunków ruchu, co często przejawia się widocznymi szarpnięciami maszyny i jest przyczyną przedwczesnego zużycia jej mechanizmów.
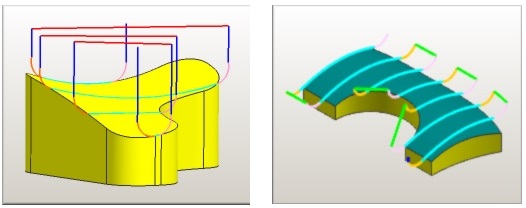
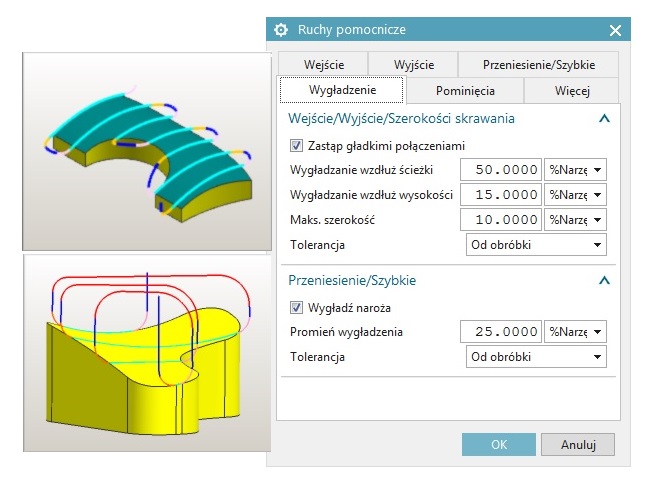
2. Naroża
Opcję naroża (rys. 3), podobnie jak wcześniejsze ustawienia, można znaleźć w większości operacji frezarskich (zarówno zgrubnych, jak i wykańczających). Zastosowanie tej funkcjonalności pozwala generować płynne ścieżki skrawające, co w obróbce szybkościowej jest koniecznością ze względu na fakt nagłych i niebezpiecznych (zarówno dla narzędzia, jak i dla maszyny) zmian kierunków frezowania. Korzyści z tego płynące, to możliwość uzyskania łagodnych i płynnych ruchów obrabiarki, generowanych (w zależności od rozpoznanej płaszczyzny pracy) z użyciem interpolacji kołowej (G2/G3) lub liniowej (G1). Dodatkowo, opcja pozwala wprowadzić limit szerokości, który decyduje o pojawianiu się dodatkowych ruchów. Funkcjonalność analizuje ścieżki narożnikowe i poprzez zwiększenie szerokości w tym obszarze wprowadza ruch „pętli”. W ten sposób zabezpieczamy się przed ścieżkami, które mogą charakteryzować się (pomimo zastosowania promienia), nagłymi zmianami kierunku.
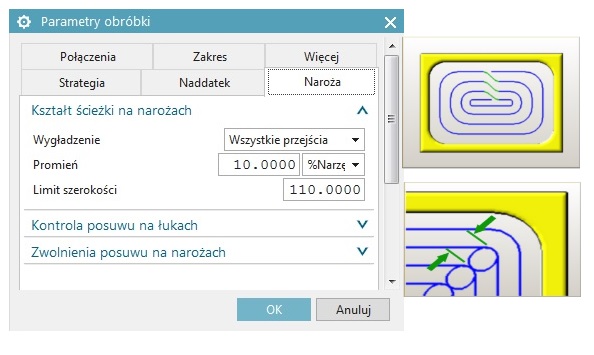
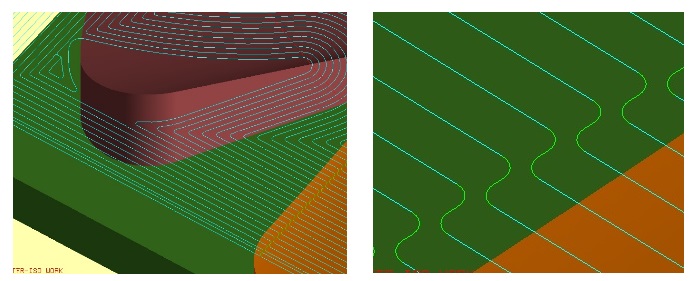
3. Trochoida
Trochoida stanowi cechę uzupełniającą technologię frezowania szybkościowego. Zaimplementowana została w systemie NX CAM w celu kontrolowania przebiegu obróbki pod kątem nagłych przeciążeń narzędzia. Charakteryzuje się tym, że w miejscach, w których zaistnieje zjawisko przekroczenia parametrów odpowiadających za szerokość skrawania, zastosowane zostaną ruchy specjalne, ruchy trochoidalne. To z kolei przekłada się na ustabilizowanie całego procesu obróbki i utrzymanie stałego zakresu obciążeń narzędzia, minimalizując tym samym ryzyko jego uszkodzenia.
W połączeniu z inteligentnym rozpoznawaniem obszarów obróbczych dostajemy kompleksową i optymalną ścieżkę narzędzia. Algorytm obliczeniowy dzieli regiony obróbki na otwarte oraz zamknięte (rys. 5), co w efekcie pozwala zastosować odpowiednią strategię wejścia narzędzia w materiał (rys. 6) i utrzymuje stałą szerokość frezowania, co jest istotnym elementem, jeżeli chodzi o trwałość narzędzia. Uzyskana w ten sposób ścieżka stanowi więc kompromis pomiędzy czasem obróbki, a kontrolowaną szerokością skrawania, rozkładając ścieżki optymalnie z podziałem na standardowe i trochoidalne, dając ostatecznie stabilny proces o stałym rozkładzie sił skrawania.


4. Jakość powierzchni obrabianej
Jak w wspomniałem na wstępie, czynników determinujących jakość powierzchni obróbki może być wiele, a jednym z nich może być odpowiednio napisany program NC, ale jak to rozumieć?
a) Rozkład punktów – w celu zapewnienia optymalnego połączenia NX CAM ze sterowaniem maszyny, mamy do dyspozycji specjalną funkcję optymalizacji, w ramach której otrzymujemy ścieżki z „uporządkowanym rozłożeniem punktów” (rys.7). Funkcjonalność ta jest obecnie standardowym rozwiązaniem stosowanym w systemie NX i oferuje bezpośrednie korzyści podczas wykańczających obróbek frezarskich, niezależnie od rodzaju sterowania używanego przez obrabiarkę. W efekcie zastosowania funkcjonalności otrzymujemy uporządkowane rozłożenie punktów (górna połowa bloku, rys. 8), co zapewnia nam lepsze wykończenie powierzchni w porównaniu z rozkładem nieregularnym bazującym na wielkości kroku, w kolejnych przejściach narzędzia (dolna połowa bloku)

Opcja dostępna jest w ramach operacji: Contour Surface Are oraz Streamline.
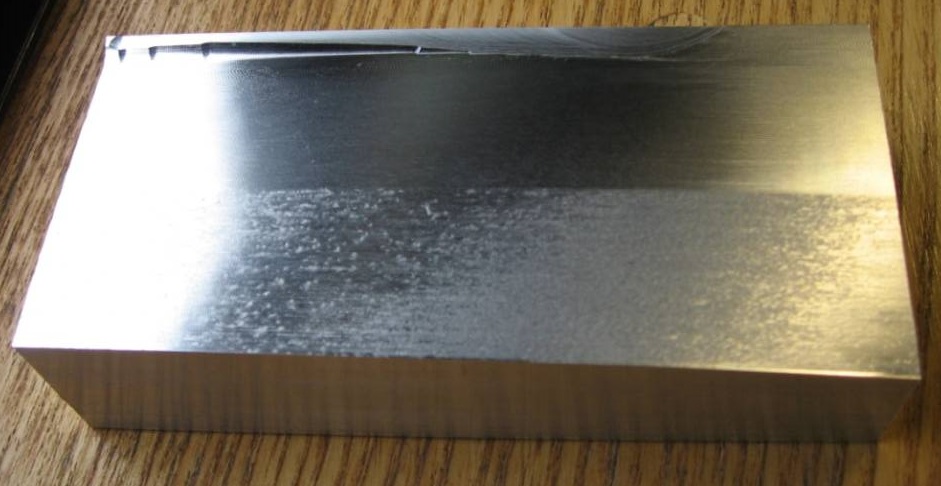
b) Interpolacja kołowa – stanowi kolejny czynnik mający wpływ na jakość obrabianej powierzchni. Korzyści stosowania funkcjonalności przejawiają się głownie w aspekcie otrzymania gładkiej powierzchni obrabianej, bez widocznych śladów przejść narzędzia – w kodzie NC mają wtedy zastosowanie łuki, a nie linie. Dodatkowym plusem tego rozwiązania jest zdecydowanie krótszy program obróbczy, co ma bezpośrednie przełożenie na mniejszy rozmiar pliku NC. Jest, to szczególnie przydatne w przypadku starszych sterowań, o małych zasobach pamięci.
5. Kontrola posuwu
Kolejna przydatna funkcjonalność wykorzystywana w obróbkach frezowania szybkościowego (lub nawet w standardowym podejściu do frezowania), to opcja kontrolowania posuwów na łukach i w narożnikach. Precyzyjnie określane zachowania się narzędzia w tego typu przypadkach, może mieć znaczący wpływ na czas obróbki, jak również na żywotność narzędzia. W efekcie tego jesteśmy w stanie podnieść efektywność procesu i zminimalizować koszty produkcyjne (mniejsze zużycie narzędzia daje mniej przestojów maszynowych).
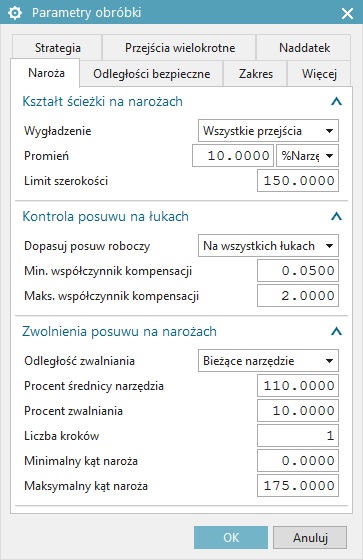
Ten punkt kończy pierwszą część artykułu na temat poprawy wydajności obróbek za pomocą NX CAM. Zapraszam do śledzenia naszego bloga. Część druga, w której opiszę zagadnienia w zakresie optymalizacji posuw, ukaże się już wkrótce.
Więcej przydatnych i praktycznych informacji na temat poprawy wydajności obróbek za pomocą NX CAM przedstawiliśmy podczas specjalnego webinarium. Zapraszamy do obejrzenia nagrania.
Opracował
Krzysztof Błachut
krzysztof.blachut@gmsystem.pl