Solid Edge Inspector: kontrola wymiarów i oznaczeń kształtu/położenia w 2D/3D
Przedstawiamy zestaw narzędzi służący do tzw. kontroli (inspekcji) zmian wymiarów i oznaczeń tolerancji kształtu i położenia w dokumentacji 2D / 3D PMI.
Mowa o rozwiązaniu Solid Edge Inspector. Zadebiutował on w Solid Edge 2023, natomiast od generacji 2024 prezentuje już na tyle rozbudowany poziom, że warto go przedstawić w odrębnym artykule.
Główne obszary zastosowań
Zadania, które wypełnia Solid Edge Inspector to przede wszystkim:
a) zbieranie informacji nt. lokalizacji i charakteru wymiarów (nominalnych i tolerowanych), a także oznaczeń tolerancji kształtu oraz położenia, na rysunkach 2D – rys. 1,
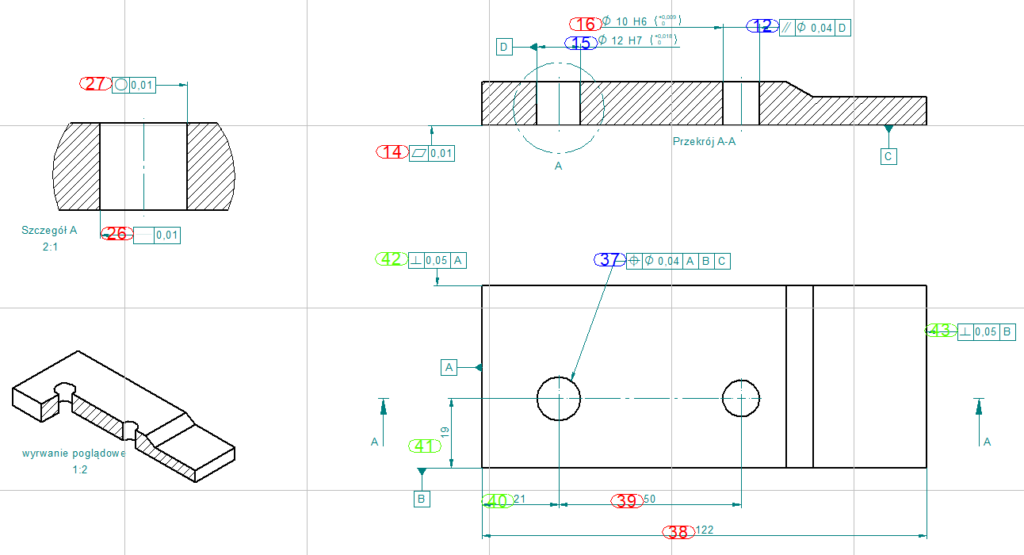
b) monitorowanie zmian ww. wymiarów i oznaczeń 2D (wartości i/lub lokalizacji), a także faktu ich ew. usunięcia / dodania nowych – rys. 2,
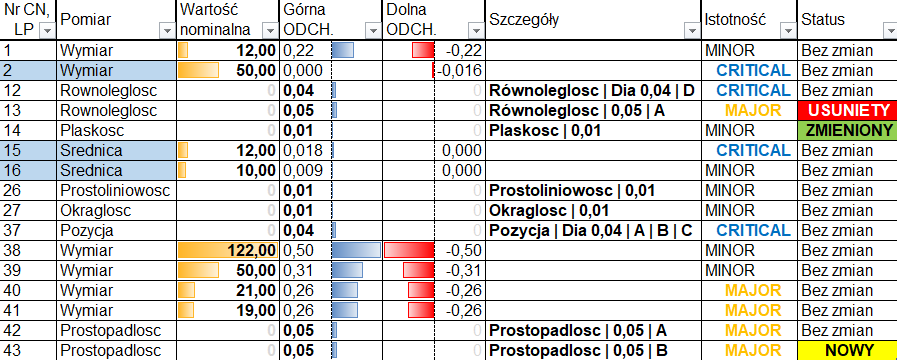
c) powyższe także dla dokumentacji 3D PMI (ang. Product Manufacturing Information, co w uproszczeniu oznacza model 3D wyrobu, w którym wprowadzono niezbędne wymiary i oznaczenia technologiczne, niezbędne dla jego wytworzenia – rys. 3.
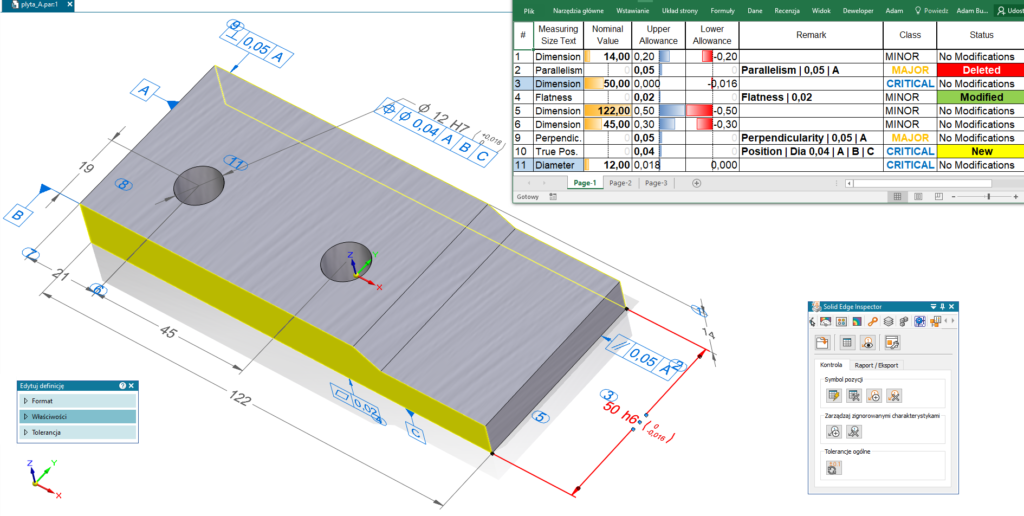
W dalszej części opracowania omówimy korzyści wynikające ze stosowania Solid Edge Inspectora w wybranych obszarach pracy z dokumentacją 2D / 3D PMI, przy rosnącym stopniu złożoności obiektów poddawanych kontroli.
Inspekcja stanu początkowego
W pierwszej kolejności przyjrzyjmy się nieskomplikowanej dokumentacji 2D, zawierającej aż i tylko wymiary o wartościach nominalnych (bez tolerancji), np. szerokość płyty 50 (jednostka mm).
Fakt, że wymiary nie posiadają tu dodatkowo sprecyzowanych tolerancji może oznaczać, iż należy je wykonać:
- w „tolerancji warsztatowej”, przyjętej przez technologa (zakład produkcyjny) lub
- w mało dokładnych (zgrubnych) klasach dokładności wykonania, np. IT14 lub
- wg normy definiującej tzw. tolerancje ogólne wymiarów liniowych oraz kątowych, np. DIN ISO 2768-1 (tj. średnia klasa tolerancji) – rys. 4.Z powyższego wyboru wynikają konkretne wartości dopuszczalnych odchyłek granicznych dla wymiarów nominalnych.
W tej części opracowania zostanie wybrana norma ISO 2768-1 m (rys. 5), w kolejnych przykładach skorzystamy także z wartości tolerancji dla IT 14.
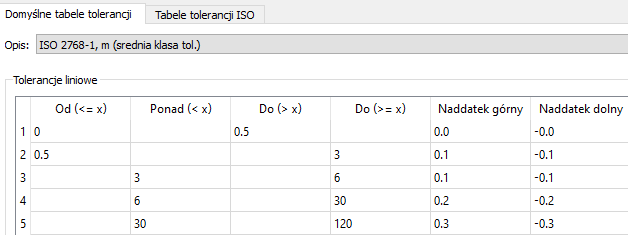
Przeprowadzając inspekcję stanu początkowego, odpowiednie oznaczenia można wprowadzać manualnie, ale zastosujemy tu sposób zautomatyzowany (całościowy). Tworząc w dokumencie ‘siatkę’ 2D, system lokalizuje każdy z wymiarów w odpowiednim polu tej siatki (np. A7 lub D5) i nadaje mu własny numer (rys. 6, warto porównać z rys. 4). Kolejność ww. numeracji wynika m.in. z lokalizacji wymiarowanego widoku rysunkowego względem przyjętego narożnika siatki.
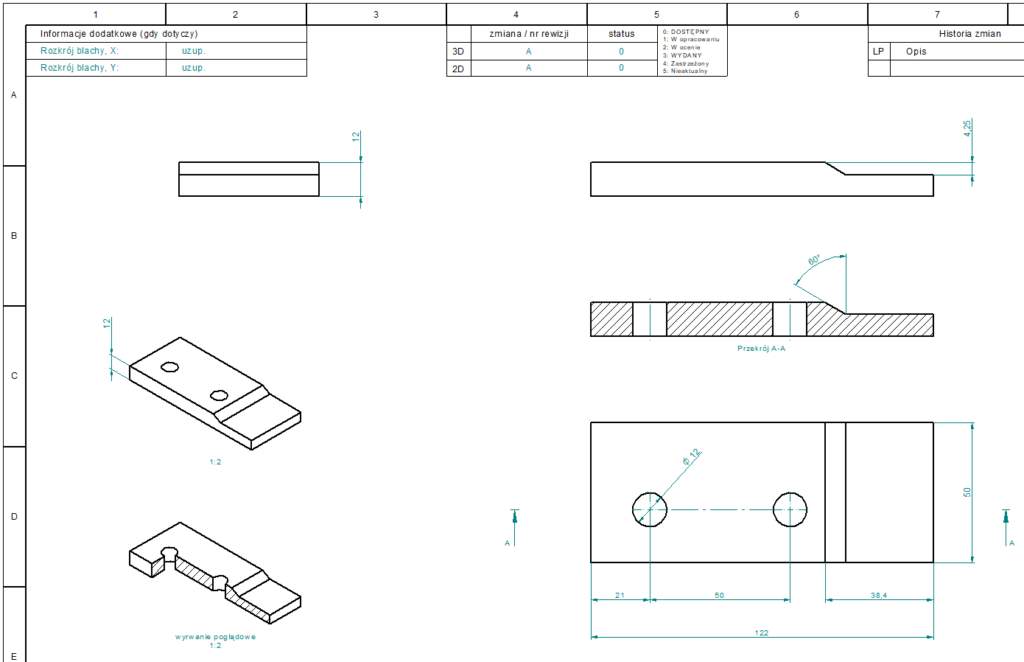
W ślad za tym idzie utworzenie zestawienia tabelarycznego dla tak zewidencjonowanych obiektów (rys. 7), które zawiera m.in.
- nr wymiaru (tzw. CN – ang. Characteristic Description/ Number),
- charakter wymiaru (długości / kąta),
- istotność („ZWYKŁY”, „WAŻNY” lub „KRYTYCZNY”, tj. szczególnie ważny),
- wartość nominalna,
- górna i dolna odchyłka wymiaru, określona tu wg wybranego standardu (jw.),
- wynikające z powyższego wartości graniczne wymiaru (górny i dolny),
- jednostka miary,
- status obiektu (w chwili początkowej – „NOWY”; podczas modyfikowania dokumentacji pojawi się status „ZMIENIONY”, „USUNIĘTY” lub „Bez Zmian”),
- nazwa arkusza …
- lokalizacja wymiaru w polu przyjętej siatki 2D.
Z poziomu tej tabeli można decydować m.in. o poziomie istotności danego obiektu, tj. zmieniać go z początkowego „ZWYKŁY”, na „WAŻNY” lub „KRYTYCZNY” (ang. odpowiednio „MINOR”, „MAJOR”, „CRITICAL”) – rys. 7.

Po dokonaniu powyższych zmian dokumentacja 2D jest aktualizowana. Przykładowo, wymiary o tak zmienionych poziomach istotności zostają wizualnie wyróżnione kontrastującymi kolorami (ww. rys. 6 w porównaniu z rys. 4).
Istnieje kilka sposobów wyeksportowania tak zestawionych informacji. Jednym
z nich jest eksport ww. tabeli do arkusza kalkulacyjnego EXCEL (rys. 8), gdzie po nadaniu prostego formatowania można uzyskać czytelne zestawienie o dużej intuicyjności wizualnej. Warto porównać rys. 8 z rys. 7.

Zmiana geometrii 3D – aktualizacja wymiarów w dokumencie 2D
Jednym z kluczowych zadań Solid Edge Inspectora w procesie rozwoju modelu 3D i aktualizowania jego dokumentacji 2D jest każdorazowe wskazywanie:
- obiektów, które obiekty uległy zmianie,
- jaki był charakter tej zmiany,
- obiektów, które nie uległy zmianie.
Załóżmy, że modyfikacja modelu 3D polegała na zmianie położenia dwóch otworów (wg osi X) o identycznej średnicy, co z punktu widzenia dokumentacji wykonawczej 2D oznacza, iż doszło do:
W przypadku wymiarów rejestrowane są m.in. ich następujące modyfikacje:
- zmiana wartości nominalnej,
- zmiana tolerancji,
- zmiana lokalizacji,
- USUNIĘCIE,
- DODANIE NOWEGO.
System rejestruje także analogiczne zmiany dla oznaczeń tolerancji kształtu
i położenia, co będzie przedstawione w dalszej części artykułu.
Załóżmy, że modyfikacja modelu 3D polegała tu na ZMIANIE położenia dwóch otworów (wg osi X) o identycznej średnicy, co z punktu widzenia omawianej dokumentacji wykonawczej 2D oznacza, iż doszło do takich zdarzeń, jak (rys. 9):
- zmiana wartości nominalnej dwóch wymiarów (21 zmieniony na 60 mm, a 50 na 14 mm – wg osi X),
- zmiana położenia jednego wymiaru (skutkiem ww. zmian, wymiar średnicy ⌀12 mm otworu ‘z lewej strony’ został wyraźnie przesunięty w prawą stronę).
Co więcej, w dokumentacji tej:
- dodano wymiar (brakujący 19 mm, tj. położenie otworów wg osi Y), rys. 9.
- usunięto wymiar (nadmiarowy 12 mm, tj. zdublowany wymiar grubości płyty), widoczny w kwadracie C1 na rys. 6.
Warto spojrzeć na rys. 9 („po zmianie”) i porównać go z rys. 6 („przed zmianą”).
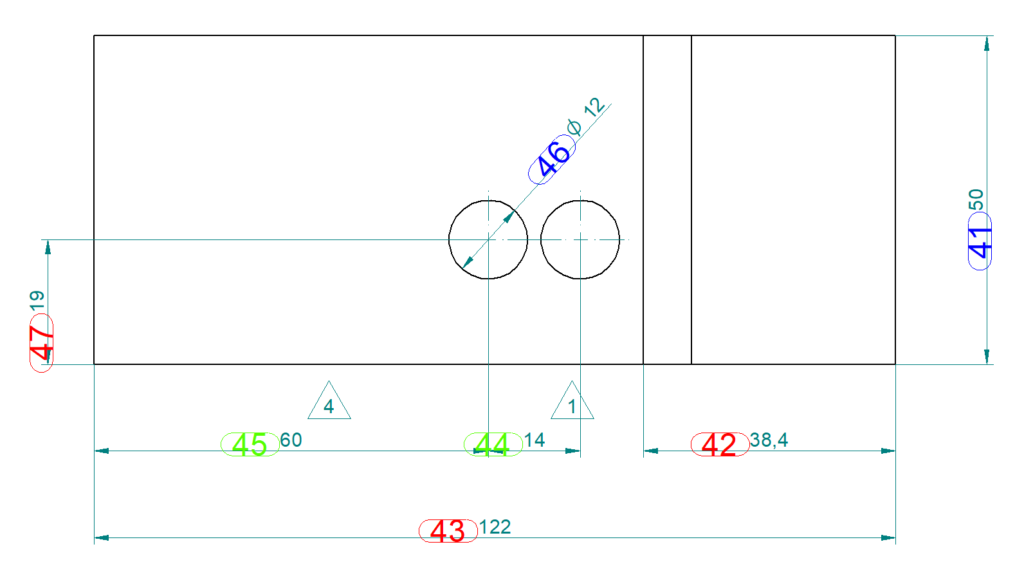
Po wprowadzeniu ww. zmian proces inspekcji został przeprowadzony ponownie (dla stanu ‘po zmianie’, in. dla kolejnej rewizji).
Solid Edge Inspector ewidencjonuje wszystkie powyższe zmiany, co można zauważyć w opisywanej już tabeli, której wyeksportowaną i odpowiednio sformatowaną zawartość (+ uwagi użytkownika) przedstawiono na rys. 10.
Tu szczególną uwagę zwracają informacje dotyczące statusu wymiarów, tj.:
- ZMIENIONY,
- NOWY,
- USUNIĘTY,
- Bez zmian.
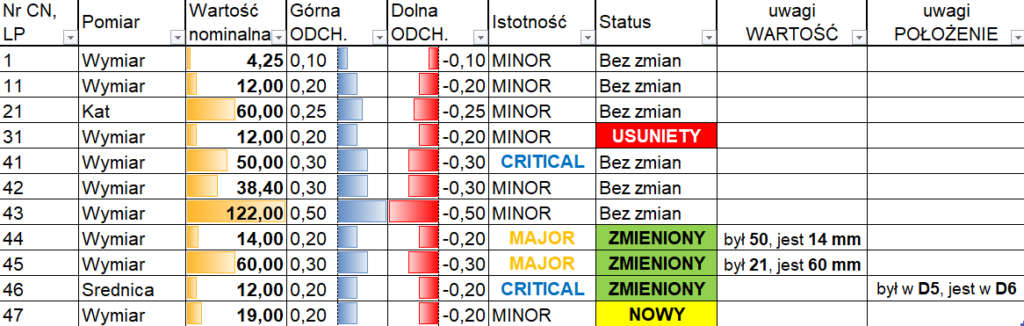
Tak uzyskane zestawienie tabelaryczne okazuje się być wyjątkowo przydatnym źródłem informacji, uzupełniając efekty klasycznego porównywania rysunków 2D (przed zmianą / po zmianie) – jak na rys. 11.
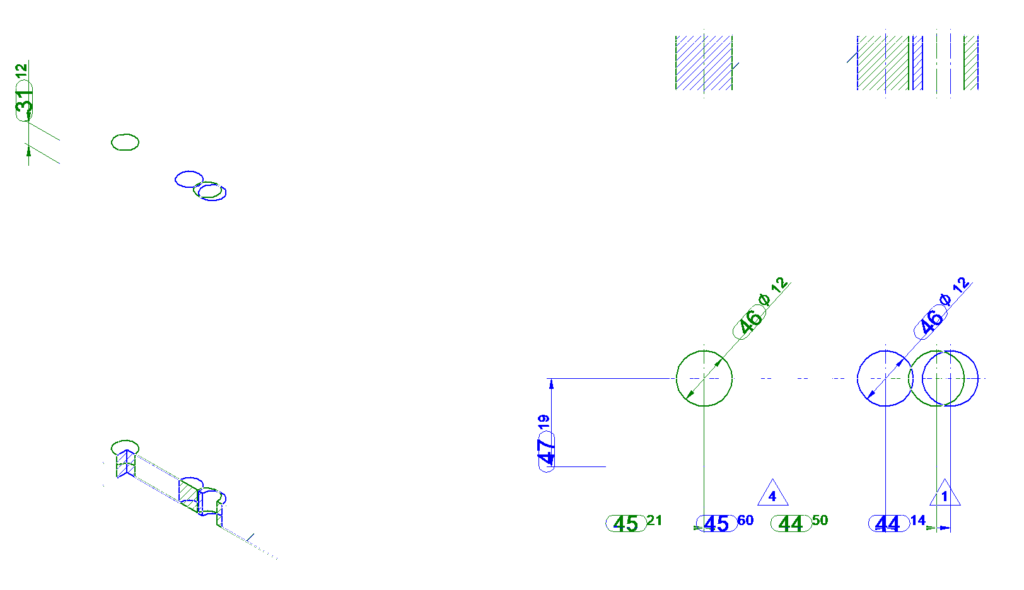
Praca z wymiarami z tolerancją jednostek
Rozbudowując wybrane wymiary nominalne o tzw. tolerancję jednostek możemy uzyskać wymiary o rożnych kombinacjach odchyłek zerowych, dodatnich i ujemnych, np.
122 +3/-2,
50 0/-1,
21 -1/-2
19 +1/+0,5.
Przejdźmy od razu do zmodyfikowania tej dokumentacji i przedstawmy efekt jej inspekcji już dla wersji ‘po zmianie’, czyli takiej, gdzie (rys. 12):
- zmieniono wartości odchyłek wymiaru (50 0/-1 na 50 +2/+1),
- usunięto wymiar średnicy (⌀12 otworu z widoku ‘z góry’),
- dodano wymiar średnicy (ściśle – „przeniesiono” ww. średnicę ‘na przekrój’, widoczny m.in. na rys. 6).
Poza tym:
- zmieniono wartość nominalną jednego z wymiarów (21 na 23 mm).
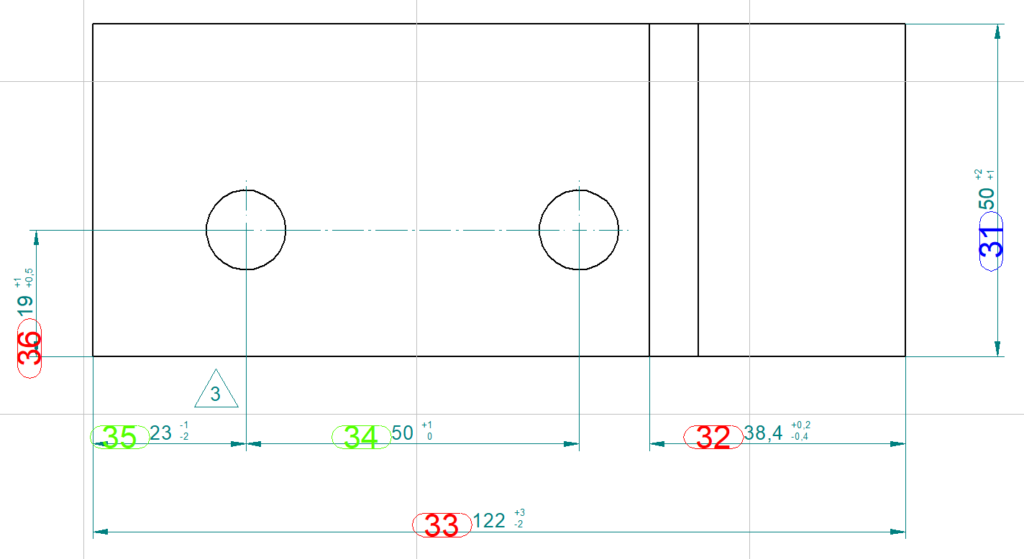
Całość i tych zmian zostanie zewidencjonowana we właściwej tabeli (rys. 13).
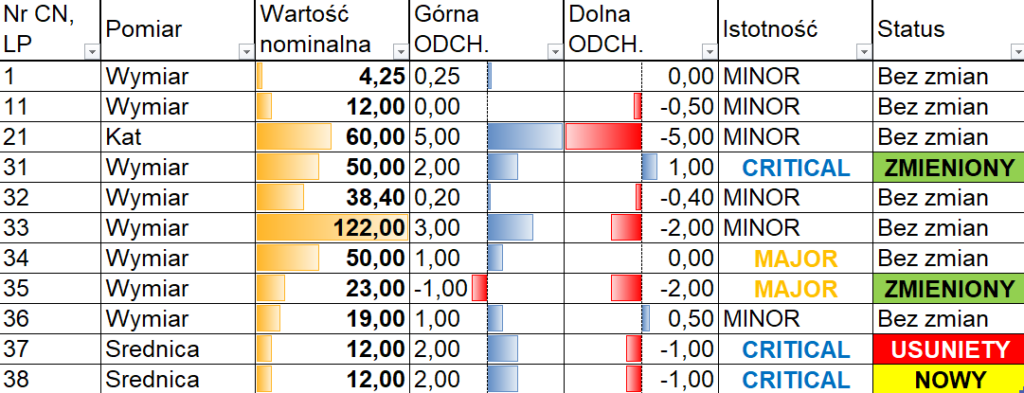
Praca z wymiarami typu ‘klasa’
Wprowadźmy do dokumentacji także wymiary typu klasa (tj. wymiar nominalny wraz z symbolem rodzaju tolerancji i klasą dokładności wykonania), np.
50 h6,
⌀12 H7,
122 n6,
12 f7.
Prowadząc zmiany analogicznie jw., rozszerzymy je o taką jak (rys. 14):
- zmiana klasy dokładności wykonania (50 h6 na 50 h7).
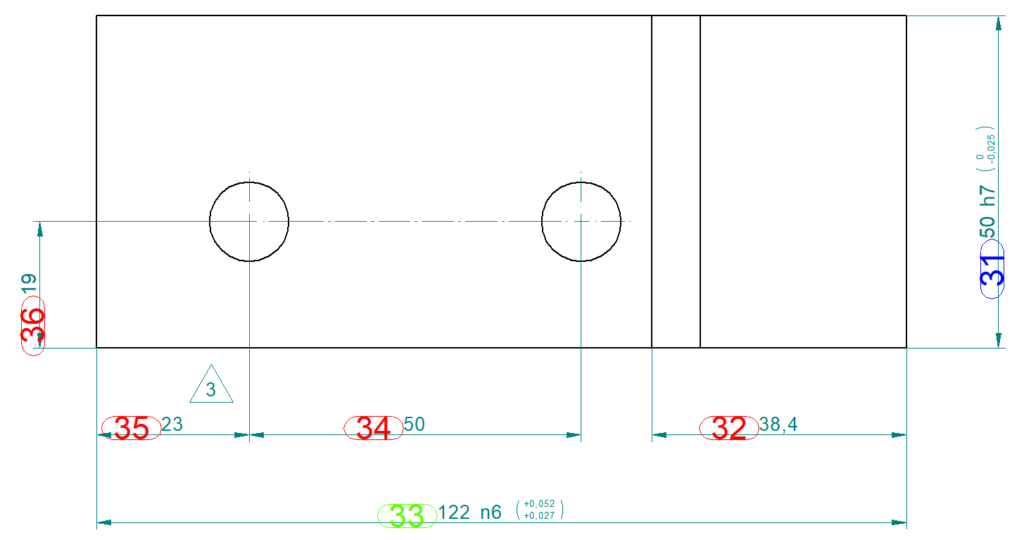
Zaktualizowane tabele inspekcji dla tego przypadku przedstawiono na rys. 15 i 16.

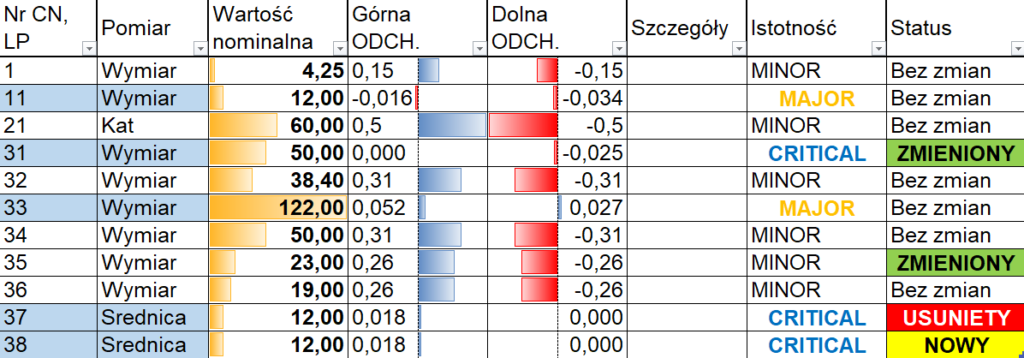
Tolerancje kształtu i położenia
Naturalnie uwzględnimy w omawianym projekcie także tolerancje kształtu oraz położenia, przykładowo (rys. 17)
- kształtu: prostoliniowość, okrągłość i płaskość,

- położenia: równoległość, prostopadłość i pozycja.
Do zmian analogicznych jw., dodajmy także następujące modyfikacje (rys. 18):
- zmieniono zakres tolerancji, np. dla płaskości z 0,02 na 0,01,
- usunięto tolerancję np. równoległości wybranego lica do bazy A,
- dodano tolerancję np. prostopadłości lica do bazy B, wartość bez zmian.
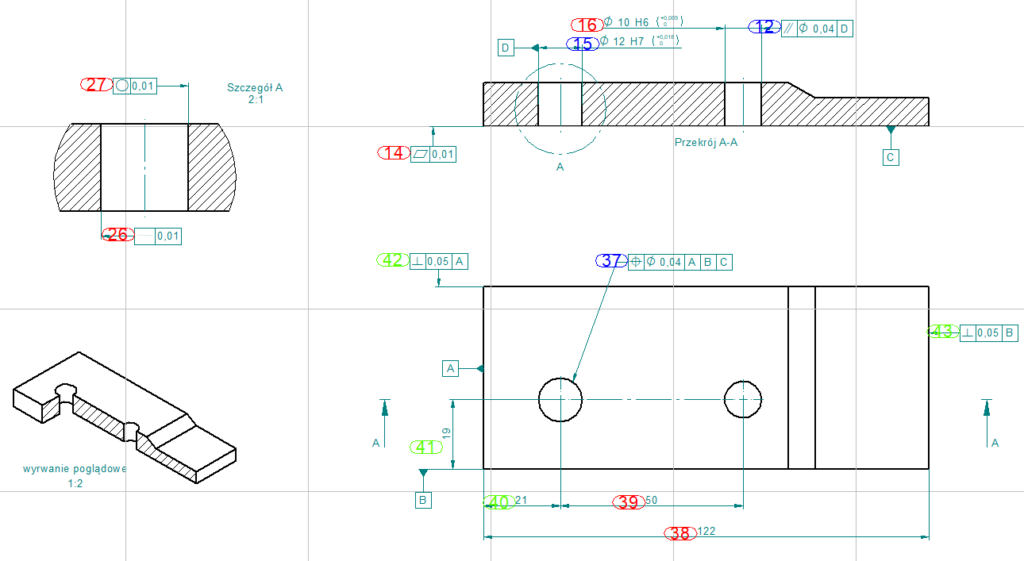
Także i tutaj tabele inspekcji zostaną odpowiednio wypełnione i zaktualizowane. Pamiętajmy, że mogą one być formatowane wg uznania użytkownika (rys. 19).
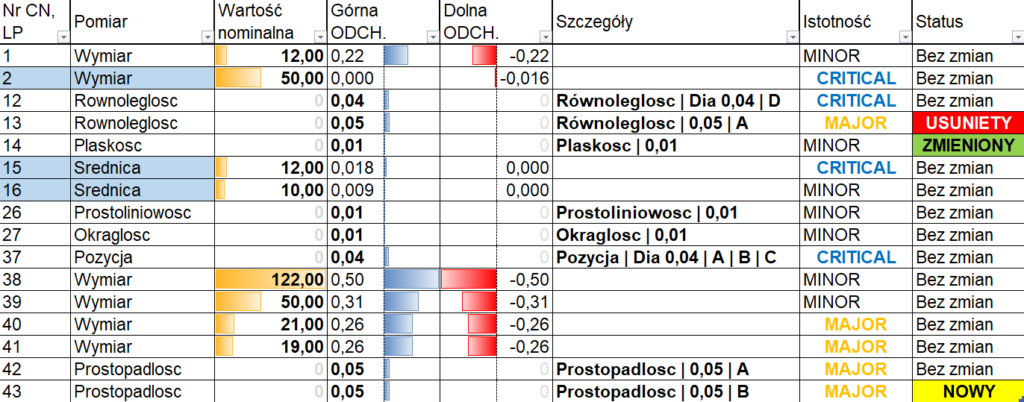
Czy tylko 2D ? Co z modelami 3D ?
Przedstawione tu zadania inspekcji (kontroli) zmieniającej się dokumentacji można realizować zarówno dla klasycznej dokumentacji 2D (powyżej), jak i dla modeli 3D z wymiarami i oznaczeniami tolerancji kształtu i położenia w standardzie PMI (rys. 20). Dotyczy to również modeli 3D elementów z blach (rys. 21).
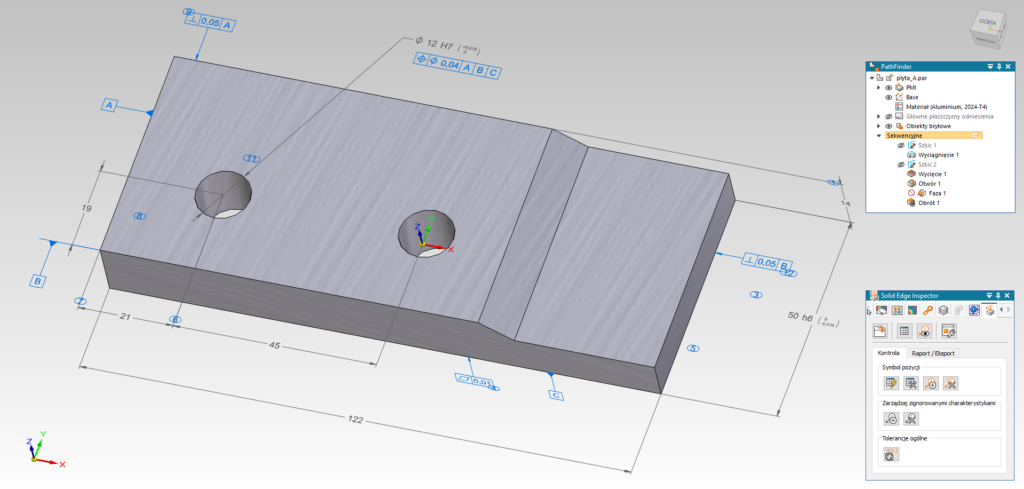

Personalizacja środowiska pracy Solid Edge Inspector
Omawiane rozwiązanie może być łatwo dostosowane do wymagań Użytkownika.
Pamiętając, że w GM System posiadamy spore doświadczenie w tworzeniu polskiej wersji Solid Edge, pragniemy przedstawić kilka obszarów, gdzie dokonaliśmy przykładowej personalizacji (‘customizacji’) środowiska pracy Inspectora:
a) dodawanie i edycja własnych standardów inżynierskich, np. norm opisujących tolerancje ogólne (rys. 22),
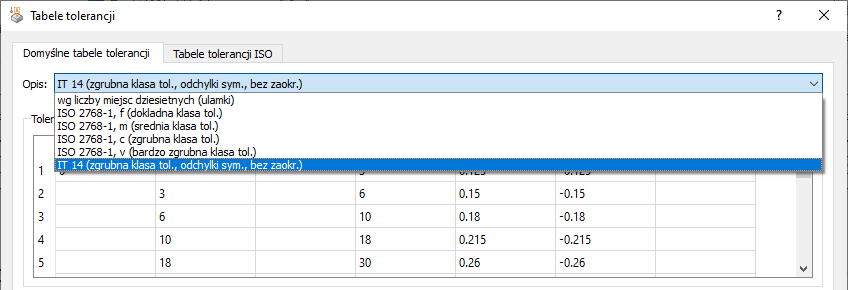
b) lokalizowany interface użytkownika in. dla tabel z inspekcji (rys. 23),

c) lokalizowany szablon raportów EXCEL oraz ich formatowanie (rys. 24).

c.d.n.
Tolerancje, a co z pasowaniami?
Dla opisywanych prac konstrukcyjnych, poza Solid Edge Inspector, firma
GM SYSTEM oferuje także
„Kalkulator tolerancji i pasowań Excel + CAD 2D/3D”
Jest to nasze autorskie narzędzie wspierające inżynierów podczas projektowania współpracujących ze sobą części maszyn (dla określonego charakteru ich połączenia i z wymaganą dokładnością).
„Kalkulator” służy do szybkiego i czytelnego przeanalizowania warunków współpracy w połączeniach wałków i otworów wykonanych z określonym położeniem pól tolerancji (względem wymiaru nominalnego) w wybranych klasach dokładności.
Narzędzie podaje wartości obliczonych luzów / wcisków i na ich podstawie orzeka rodzaj pasowania tych obiektów (luźne, ciasne, mieszane).
Głównym elementem „kalkulatora” jest arkusz XLSX (rys. 25, 26, 27).

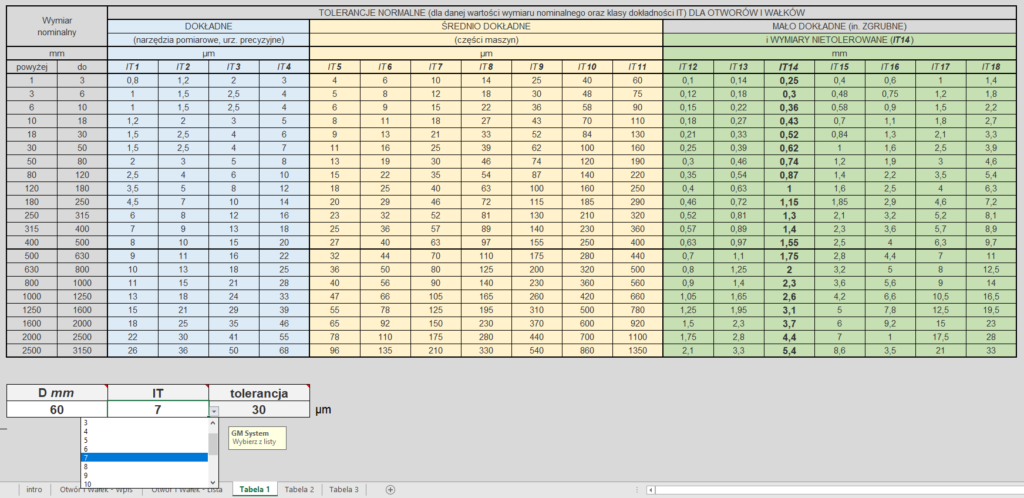
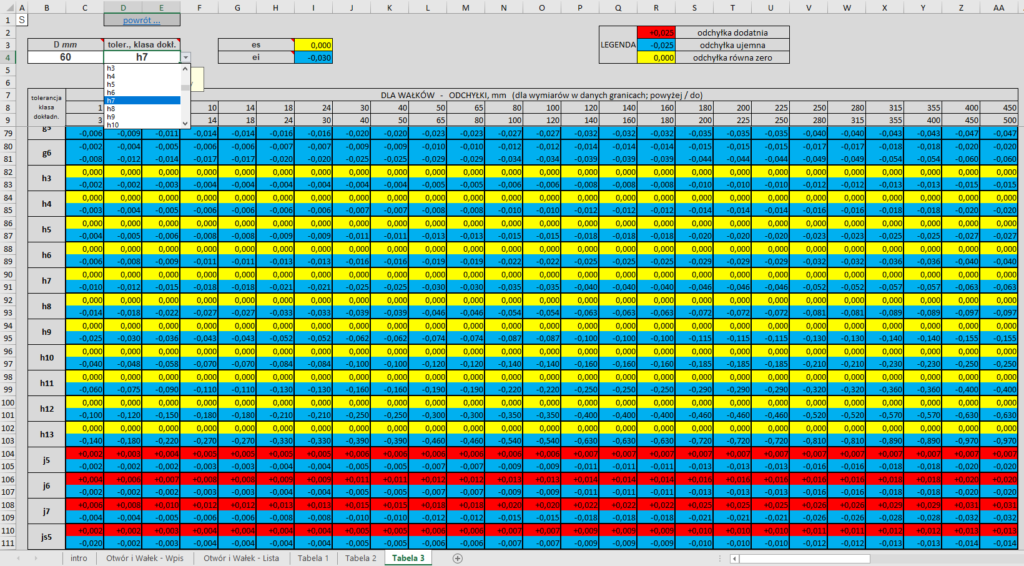
Efekty dokonanych obliczeń są przedstawiane także w CAD Solid Edge, zarówno w 2D, jak i w 3D (rys. 28).

Więcej informacji na temat ‘kalkulatora’ można uzyskać w CENTRUM WSPARCIA firmy GM SYSTEM, klikając w ten link.
Podsumowanie
Stosowanie INSPECTORa ma na celu osiągnięcie następujących korzyści:
- czytelne zwrócenie uwagi na ważne cechy geometryczne wyrobu,
- zebranie danych o kluczowym znaczeniu dla wytwarzania i eksploatacji produktu (wymiary tolerowane, oznaczenia tolerancji kształtu i położenia),
- stosowanie standaryzacji prowadzącej m.in. do ujednolicenia oraz uproszczenia technologii produkcji (np. dla wymiarów bez tolerancji),
- automatyzacja ww. zadań, tj. zmniejszenie ryzyka ludzkiego błędu
podczas ich realizacji (niedopatrzenie, błędne tolerancje, etc.), - ’monitorowanie’ dokumentacji z rejestracją dokonywanych zmian,
- zmniejszenie strat materiałowych, narzędziowych i czasu,
- zapewnienie wyraźnych zysków przez eliminację strat i opóźnień.
Opracował:
dr inż. Adam Budzyński
Jako GM System aktywnie prezentujemy nowości pojawiające się w środowisku Solid Edge. W ostatnim czasie zorganizowaliśmy tematyczny webinar, podczas którego dr inż. Adam Budzyński, lider zespołu CAD w GM System, szczegółowo przedstawił najważniejsze funkcje Solid Edge Inspector, bazując na konkretnych przykładach. Zapis webinaru można odebrać na stronie www.seinspector.gmsystem.pl
Nasi inżynierowie są do Państwa dyspozycji. Tych z Państwa, którzy są zainteresowani wdrożeniem w swoich organizacjach Solid Edge Inspector, zapraszamy do kontaktu. Chętnie porozmawiamy, podpowiemy, przedstawimy zalety poszczególnych rozwiązań, a w razie potrzeby wesprzemy w doborze produktu najlepiej odpowiadającego Państwa potrzebom.