PLM jako źródło wymiernych korzyści
Oprogramowanie klasy PLM stanowi element strategii zarządzania firmą, skutecznie umacniający jej pozycję w stosunku do konkurencji. Kiedy powinno się rozważać wdrożenie PLM/PDM, jakie może to przynieść korzyści i czy jest to optymalna strategia dla każdej firmy?
W jednym z poprzednich artukułów publikowanych na naszym blogu opisałem, jakimi atutami dysponuje oprogramowanie SIEMENS Teamcenter Rapid Start™, tematem niniejszego opracowania jest natomiast przedstawienie korzyści płynących z zastosowania systemu PLM.
Obecny dynamiczny rynek wprowadza szereg coraz to nowych wyzwań dla firm produkcyjnych. Niekończący się wyścig technologiczny kieruje procesem produkcyjnym w bardzo skomplikowany sposób i dotychczasowe budowanie przewagi na podstawie prostych metod nie jest już skuteczne.
Co to jest PDM/PLM?
PLM (z ang. Product Lifecycle Management) to strategia opracowana na potrzeby bardzo dużych firm produkujących rodziny skomplikowanych produktów. Główną zaletą takiego rozwiązania jest szeroki zakres implementacji oraz względnie łatwa rozszerzalność.
PDM (z ang. Product Data Management) to strategia wspomagająca przedsiębiorstwa średniej wielkości, w których produkty i ich rodziny nie wymagają zastosowania pełnego zakresu zarządzania. Jeśli firma będzie się rozrastać, implementacja ta pozwoli na późniejszą aktualizację do pełnego oprogramowania PLM, a system importu danych pozwala na przeskanowanie obecnych danych i wyszukanie kolizji w plikach jak i ich brak.
Patrząc na rynek z perspektywy lat można zauważyć, że firmy decydując się na system PLM/PDM kierują się następującymi potrzebami:
Firmy, które obecnie wykorzystują PLM/PDM i chcą dalej korzystać z dobrodziejstw tej strategii motywuje:
Jak widać potencjał aplikacji rośnie w miarę jej wykorzystania i pozwala na zauważenie dotąd nieuchwytnych szczegółów okołoprojektowych, które świadczą o sukcesie.
Kiedy zdecydować się na PLM/PDM?
Głównymi symptomami świadczącymi o potrzebie takiego wdrożenia są:
- Niedostateczny, nieefektywny system wymiany danych między oddziałami sprzedaży, produkcji, marketingu.
- Coraz większy „gąszcz” w plikach projektowych. Widomo nie od dziś, że niejednokrotnie zdarza się wykonywać prace odtworzeniowe zagubionych dokumentacji CAD.
- Zwiększenie częstotliwości oraz różnorodności produktów, co przekłada się na ich podwyższony stopień złożoności.
- Zwiększające się koszty produkcji produktów.
- Nieterminowość realizacji zamówień.
- Brak identyfikacji wyrobów, jak i ich części składowych.
Są to jedne z głównych objawów braku systemu PLM/PDM.
Zdajmy sobie sprawę, że na sukces firmy składa się więcej czynników i są one różne dla każdej z branż.
Dla jednych będzie ważna dystrybucja oraz terminowość, inni borykają się z zasobami magazynowymi, czy z dokumentacją produkcyjną. Niewątpliwe jest jednak to, że system PDM/PLM wspiera wszystkie wspomniane zagadnienia i pozwala na sprawne zarządzanie nimi bez przerw – całą dobę, przez cały tydzień.
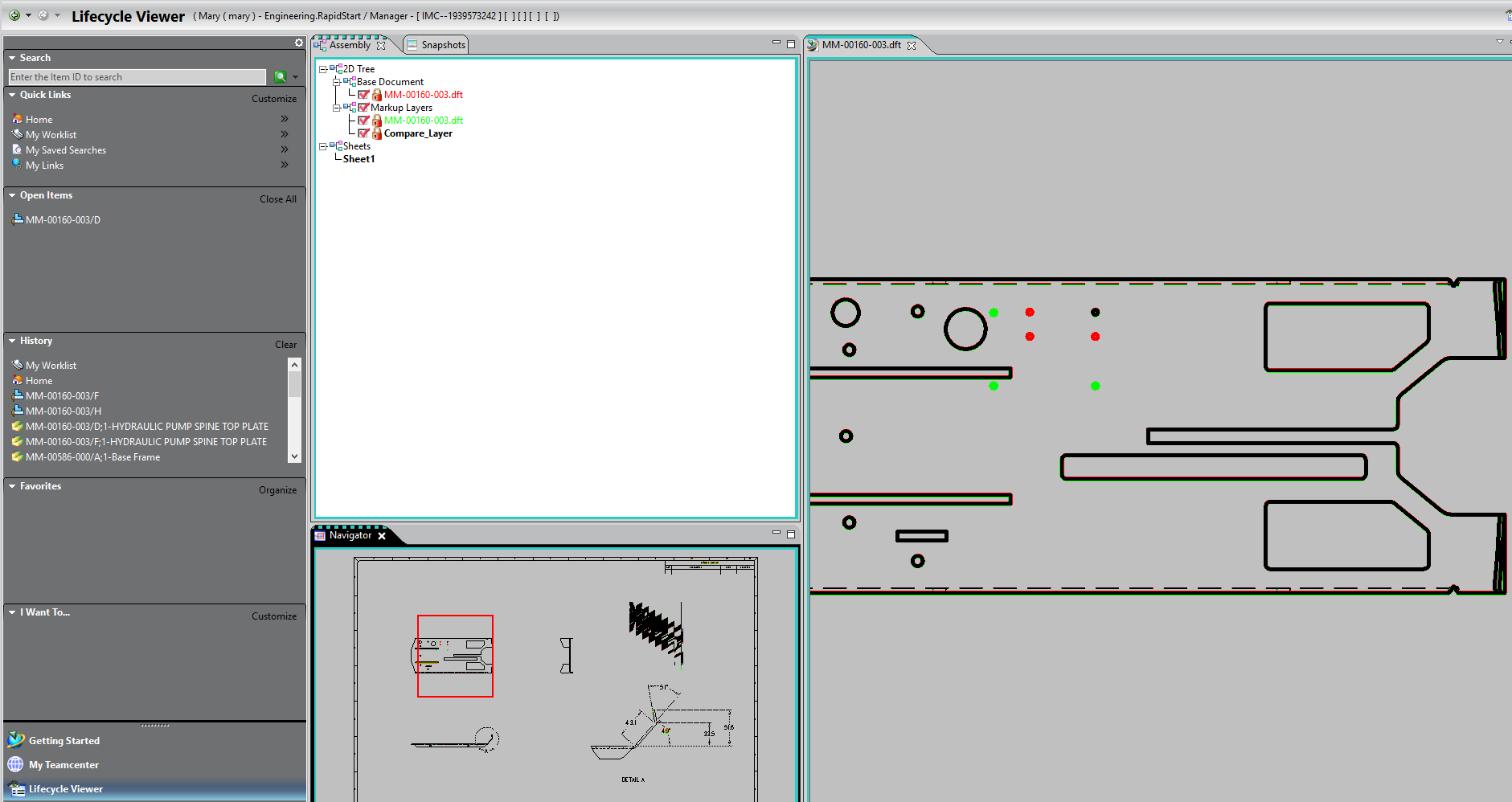
Implementacja
Podobnie, jak w każdym przedsięwzięciu IT, najważniejszym etapem wdrożenia jest analiza potrzeb i ryzyka z nim związanego. Bez tego kluczowego procesu implementacje przeprowadzane są na ogół niedokładnie mijając się z celem klienta i narażając całe przedsięwzięcie na szkody.
Istnieje wiele metodologii, jakimi można się posłużyć przy wdrożeniu, jedną z nich jest analiza i stworzenie wzorca wymagań/możliwości. Następnie zainstalowanie oprogramowania „z pudełka” i korzystanie z niego w formie, jaką przewidział producent, a po pewnym czasie odpowiednie modyfikacje środowiska na szczególne potrzeby firmy. Takie podejście pozwala nam na szybkie przejście na nowy system i migrację kluczowych projektów.
Warto pamiętać, że wdrożenie strategii PLM/PDM ma służyć na lata jako spoina wiążąca poszczególne działy organizacji.
—Case Study———————————————————————————————————–
Jako przykład udanego wdrożenia chciałbym przedstawić historię firmy, która postanowiła wdrożyć oprogramowanie Siemens Teamcenter.
HINO MOTORS™
Hino Motors™ jest japońskim producentem samochodów ciężarowych, który jako pierwszy zaprezentował jednostkę transportową zasilaną w pełni prądem elektrycznym. Firma zaopatruje w swoje produkty nabywców z 80 krajów.
Przed zastosowaniem strategii PLM/PDM inżynierowie wykorzystywali w swojej pracy oprogramowanie CAD CATIA® oraz Creo®. Zarządzanie dokumentacją odbywało się za pomocą standardowych rozwiązań systemowych (pliki, foldery) jak i dedykowanego systemu zarządzania dokumentacją CAD tylko dla jednej z dwóch technologii. Stwarzało to chaos informacyjny podczas przepływu oraz wymiany danych między dwoma działami projektowymi.
Hino Motors™ w swojej ofercie posiada wiele wersji tej samej ciężarówki różniących się np. miejscem montażu zbiornika paliwa. W rzeczywistości osiągnięcie tych wariantów wiąże się tysiącami zmian projektowych. Inżynierowie tworzący wyposażenie takie, jak akumulatory i baki, muszą współpracować z innymi projektantami, aby zachować kompatybilność całego zespołu. Jeżeli pozycja baku zmieni się jest to równoznaczne ze zmianą części w ponad 100 modelach tego samego samochodu ciężarowego w tym samym czasie. Dlatego tak ważne jest, aby te zunifikowane informacje powinny być zarządzane.
W czasie, kiedy firma zaczęła eksportować swoje produkty na rynki obce, pojawił się następny czynnik definiujący finalny projekt zespołu, jakim jest prawo lokalne odbiorcy. Idąc tym tropem możemy zauważyć, że pogoda również stanowi wyznacznik zmian technologicznych, jakie trzeba nanieść, aby być dopasowanym do lokalnych potrzeb.
„Części, które są obecnie projektowane, używane są w innych projektach, więc jeżeli coś się w nich zmieni musi być o tym wiadomo” mówi Toshiaki Miyashita zastępca głównego menadżera Hino Motors CAD. W tak zawiłym procesie projektowym, ciężko sobie wyobrazić pracę bez systemu do zarządzania tą masą informacji.
Przed wdrożeniem Teamcenter, 73% projektantów zgłosiło, że miewali poważne problemy z dokumentacją. Największym problemem było uzyskanie dostępu do aktualnej wersji modelu, na którym mają pracować. Miewali również problemy z jej udostępnianiem.
Kluczowymi powodami dla wybrania oprogramowania Teamcenter były:
- zunifikowany proces zarządzania najświeższymi wersjami danych,
- możliwość przeglądania dużych złożeń za pomocą lekkiej przeglądarki nie wymagającej oprogramowania CAD,
- zarządzanie częściami używanymi w różnych projektach w dwóch różnych technologiach CAD.
Po wdrożeniu oprogramowania Teamcenter firma zauważyła znaczący wzrost wydajności projektantów. Dotychczas, aby wprowadzić zmiany w 10 projektach potrzeba było tygodnia i dwóch inżynierów. Natomiast po wdrożeniu ci sami inżynierowie są w stanie nałożyć poprawki w 60 maszynach. Daje to 12-krotny zysk wydajnościowy.
Integracja środowiska Siemens Teamcenter® software pozwoliła firmie na dostęp do najświeższych dokumentacji w każdym czasie.
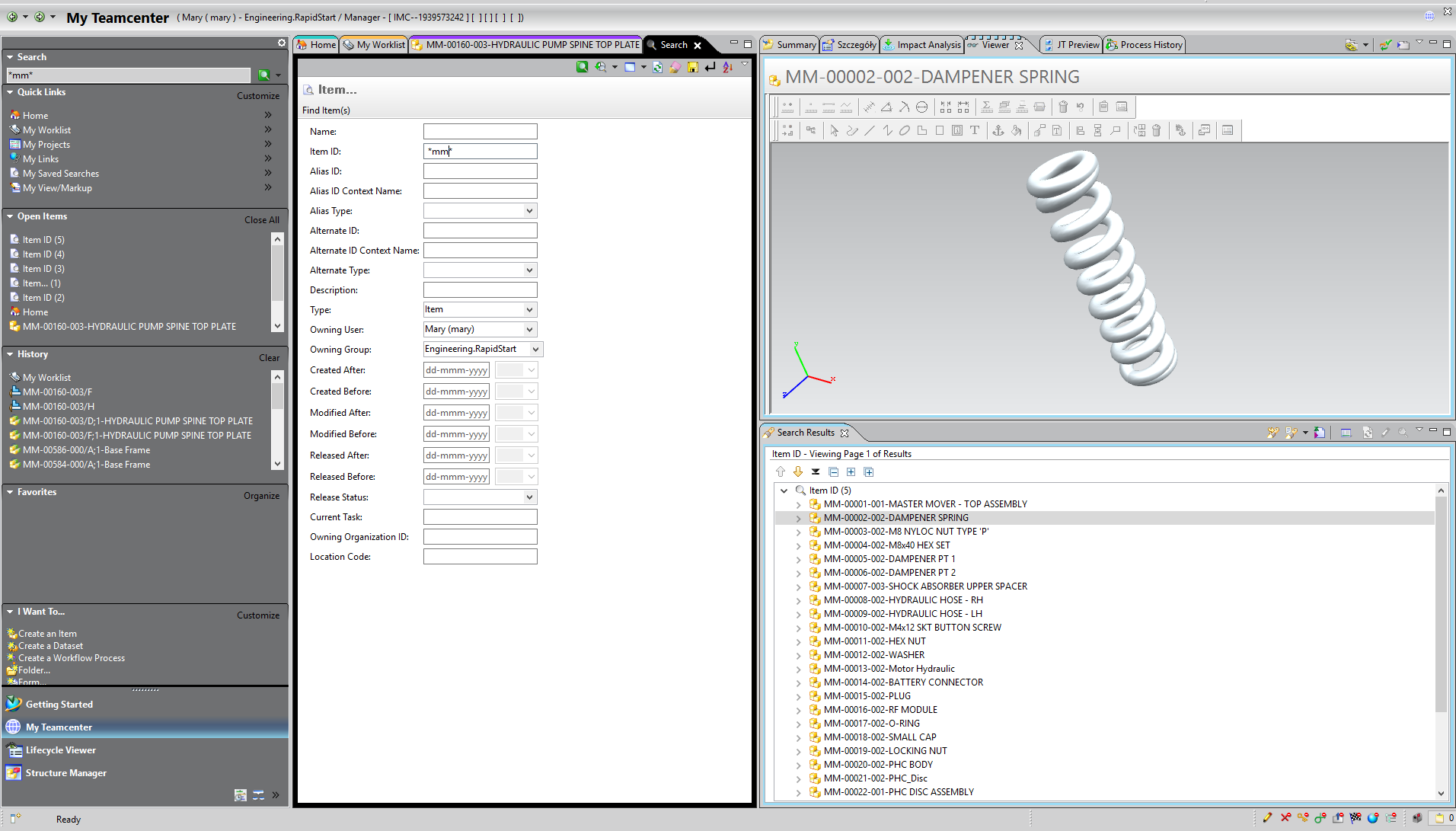
Poza redukcją czasu, firma rozwiązała wiele problemów powstających w czasie projektowania. Proces podzielony jest na cztery oddzielne etapy. Przed wdrożeniem, niedociągnięcia projektowe były zauważalne aż do czwartego etapu. Jednakże przy pomocy oprogramowania, wszystkie problemy twórcze są poprawiane do trzeciego etapu, który zawiera w sobie projekty form wtryskowych i którego każdorazowe modyfikacje są bardzo kosztowne. Zauważalnie wzrosła również jakość produktów, a całościowe koszty zostały zredukowane.
Niedawno firma wypuściła na rynek nowy model samochodu ciężarowego HINO 500 Ranger. Jest to pojazd trzeciej generacji oparty na innej platformie niż poprzednie generacje, które produkowane są w indonezyjskiej fabryce.
„Nie byli byśmy w stanie tego dokonać bez wsparcia platformy Teamcenter”, mówi Miyashita.
Jest to pierwszy projekt, który został stworzony w Japonii, a produkcja została uruchomiona w zagranicznej fabryce. Czas na wykonanie był ok 20% krótszy niż zwykle i drużyna projektantów zdawała sobie sprawę, że nie podołałaby temu zadaniu stosując metody konwencjonalne.
Teamcenter został zmodyfikowany i dostosowany do potrzeb klienta podczas instalacji, jednak Hino Motors bierze również pod uwagę zmianę sposoby pracy.
Miyashita tłumaczy, „Jest wiele zmian w instalacji Teamcenter, jednak utrzymanie ich również kosztuje. Chcielibyśmy wykorzystać standardowe rozwiązania dostarczone od producenta. Aby tego dokonać musimy zmienić sposób jak podchodzimy do projektu.
Dodatkowo przeglądarka JT umożliwia podgląd złożeń bez potrzeby instalowania oprogramowania CAD. Teraz projektanci konsultują najdrobniejsze zmiany na podstawie podglądu JT, a same zmiany są już dokonywane w oprogramowaniu CAD.”
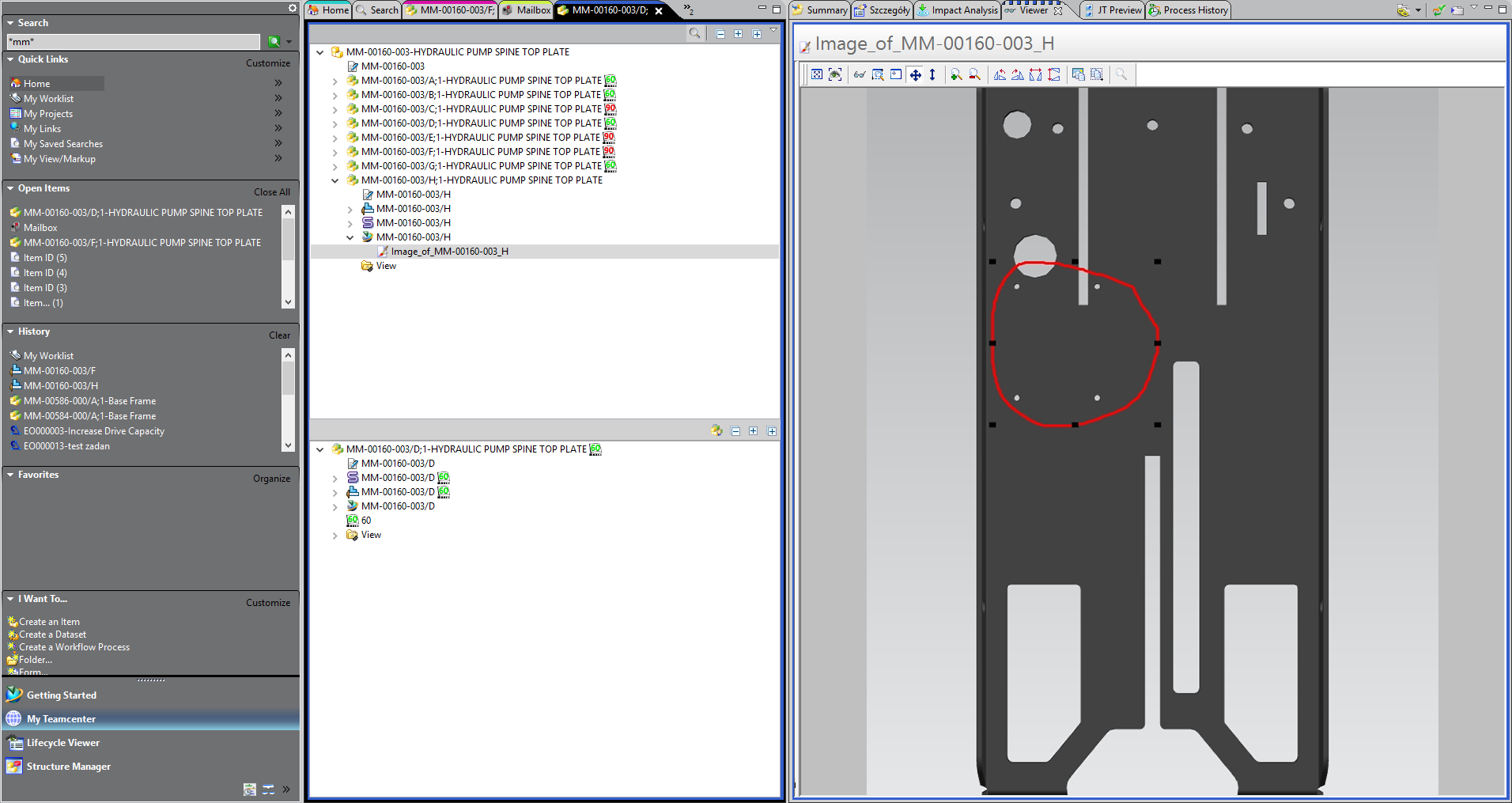
Następne kroki z Teamcenter
Nie tylko grupa projektantów otrzymała wsparcie systemu Teamcenter. Programu CAD używa się także do produkowania katalogów produktów. Poprzednio produkty były fotografowane, jednak Hino Motors jest teraz w stanie użyć plików CAD do stworzenia komputerowego renderingu wybranych produktów. Wyprodukowanie serii 10 różnych katalogów kosztuje teraz znacznie mniej niż dotychczas.
Obecnie, Hino Motors jest na etapie wdrażania Teamcenter Manufacturing w celu wizualizacji prototypów, jednak docelowo będzie on również zarządzał danymi form wtryskowych, instrukcjami obsługi, aby rozszerzyć funkcjonalność poza dział projektowy.
Firma posiada także różne typy systemów do zarządzania kosztami, a poprzez ich integrację będzie w stanie rozszerzyć system Teamcenter na cały okres życia produktu.
„Docelowo chcielibyśmy, aby dział sprzedaży miał możliwość zgrubnej wyceny oferowanych produktów na podstawie specyfikacji klienta i możliwość zlecenia ich na produkcję” mówi Miyashita.
Teamcenter Rapid Start jest swoistym pierwszym krokiem w osiągnięciu harmonii i systematyzacji w obiegu dokumentacji. Biorąc pod uwagę dużą elastyczność platformy jesteśmy w stanie zintegrować ją niemalże z każdym procesem w firmie, co końcowo umożliwia nam szybsze osiągnięcie celów i założeń, które stawiamy sobie każdego dnia.
opracował
Michał Grygonis